放开供应商,找研发要成本!
导读
国内有很多公司,谈到降成本就让供应体系找供应商过来,给定指标降幅。这样做真的好吗?任何制造业的从业者都知道,一分钱一分货,你让别人降价,就不怕质量隐患吗?
对此,我们不仅大声疾呼:放开采购,放开供应商,找研发要成本!
设计决定产品的直接成本
要降低成本,首先要从研发设计着手,其次从制造着手。
① 研发设计中降低成本
成本等于市场可以接受的产品价格减掉所获得利润,所以研发设计中就要对成本进行管理。如果研发设计不进行成本管理,就会造成以下现象:
a. 技术水平低导致过剩安全系数设计。技术水平比较低,会导致过多的逾越度和过分的安全系数设计,使单一零件的成本大于竞争对手的产品成本。
以钣金垫的设计为例,钣金垫越厚,非但不代表产品越安全,还会使单一零件成本数倍增加,更可能降低产品安全系数。比如,在生产汽车的保险杠时,如果采用非常硬的纯钢,汽车在撞击时可能不会被撞坏,但车内的人会不安全。所以,在设计钣金垫时,要考虑使用比较薄的材料,通过结构的变形吸收能量,这样产品既安全,材料的成本又很便宜,还会使产品比较省油。
b. 设计标准化、模块化程度低。设计标准化、模块化程度低,产生的零件数较多,就会增加模具和管理成本。
c. 设计时忽视工艺,不进行标准成本分析,导致产品成本高。设计人员对工艺不了解,也不进行标准成本分析,不明确需要增加多少材料费、管理费、加工组装费,设计出来的产品的成本就会很高。
② 各业务环节上降低成本
设计是影响产品成本最重要的因素。
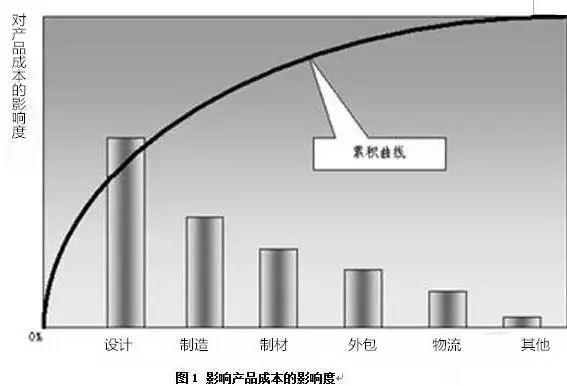
如图1所示,影响产品成本的因素包含设计、制造、制材、外包、物流及其他。制造成本最终反映在报价上,如果不包含供应商的制造成本,采购的成本就可能会高于内部制造成本。另外,包装费用、加工精度和加工费等也会影响到产品的成本。
③ 材料设计中减少成本
加工精度与加工费用成正比
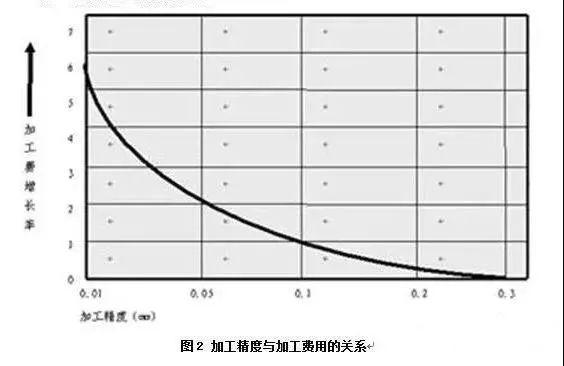
如图2所示,随着加工精度的提高,加工费用会呈指数增长。当精度提高到一个数量级,就意味着使用的设备等级越高。
原来可以使用一台几万元的设备,假如要提高加工精度,就必须使用几百万元的设备。价格不同的设备,折旧费也不同,加工成本的差别也会非常大。
难加工与易加工设计的成本差异
为了节约成本,设计时应尽量考虑容易的操作,难加工会提高很多成本。
如设计某产品,其底部是一个非常平的孔,产品成本就很高,但把它设计成平的,必须用到特殊的处理方法。如果该产品的底部是平的,就需要用特殊的工具削平,而如果把它的底部设计成三角形,只要使用钻头打孔,而不需要其他特殊处理,图3所示。
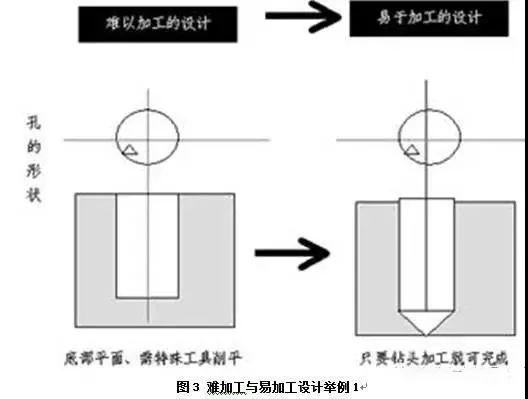
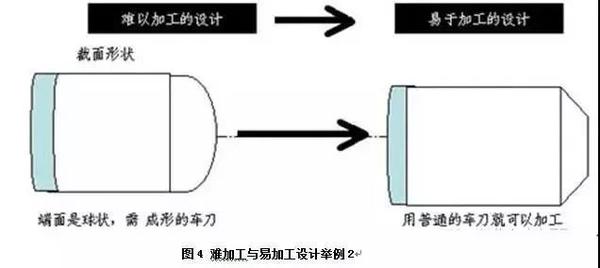
如图4所示,设计一个截面,本来的设计是圆形截面,如果把该零件的截面设计成圆形,就要开发专门刀具,这样成本就会很高;而把它的截面设计成梯形之后,就很容易制造了。
如果某项设计不是产品的卖点,不能确立产品的竞争优势,就没有必要进行设计;如果某项设计是产品的卖点,能够提高产品的价格,则可以考虑设计。
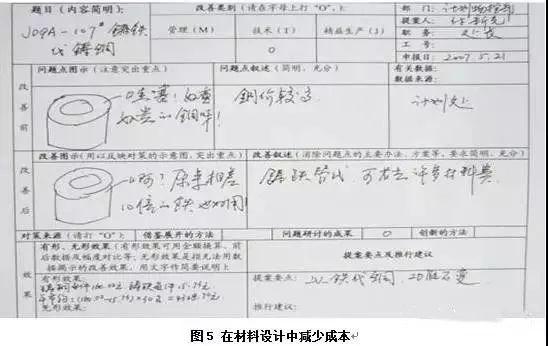
如图5所示,在材料设计中采用铜,价格高,一般为六万多元/吨,而钢才四千元/吨,而且铜的比重是8.9,钢的比重为7.8,同样一吨材料,用钢所产出的数量比用铜要多百分之十几,而且没有影响性能。所以,用钢代替铜,可以节省很多材料。

如图6所示,如果为了制造某零件将钢板掏空,就会报废掉很多材料,而如果一开始就制作铸件,直接把零件做成需要的形状,就不会浪费材料。
通过以上的例子,可以得出三点启示:
第一,设计人员熟悉材料和制作工艺,能够在不影响产品质量的前提下使用价格更低的材料,也有助于降低成本。
第二,设计人员要学会标准成本的核算方法,如使用什么标准材料、标准部件、需用几个工时等,能够有效控制成本。
第三,成熟产品可以系统地降低成本,一方面是因为产品批量变大,摊薄了固定费用,另一方面是进行的一些设计变更也可以减少材料的清耗。
设计的模块化
① 非卖点,不产生竞争力的地方禁出图
企业的设计开发制度和考核出了问题就会出现差异很微小的新零件和新物料。比如,以设计新产品的数量和出图纸的数量作为设计人员的业绩考核指标,就会使设计人员把一个微小的改变也当做新零件的设计,造成大量垃圾图纸出现,大大增加成本和制造时间。
成熟的设计师一般会尽量少出新图、新零件,只是对于个别有卖点的设计,必须要进行新的突破才进行修改。少出新图、新零件,模具和物料种类会比较少,库房管理就会变得容易;模具识别低,成本也会较低,而且产品的品质会非常稳定和可靠,新产品的开发时间也会大大缩短。
评价项目是否成功,不是评价这个项目出新图纸和新零件的数量,而要看是否有新的技术突破以及项目能带来的盈利和质量。所以,不是卖点,不产生竞争力的地方,企业应严禁出新图,尽可能采用已有的图纸和设计。
② 设计规范编制方法
企业要形成设计规范,规定设计的方式。比如,电源有开关电源、模拟电源等多种类型,在什么样的产品上使用开关电源,在什么条件下使用模拟电源,电阻是多少,依据什么标准,选用哪种螺丝,选用何种金属材料等,都需要进行标准化。
设计的模块化能够保证产品的生产,一流的企业都是采用标准的模块化设计。缺乏设计规范的企业,会出现设计错误较多、产品设计开发时间较长、产品质量不稳定、返工率高、产品缺点多、经济效益低等问题。
- 上一篇:精益流程改进的好处有哪些?
- 下一篇:TPM设备管理的“四化”管理