前言:标准工时是在标准工作环境下,进行一道加工工序所需的人工时间。标准工时的制定方法有多种,本文介绍一些常见的计算方法。
—1—
标准工时的三个概念
1、标准工时:在特定的工作环境条件下,用标准化的作业方法和设备,以普通熟练工作者的正常速度完成一定质量和数量的工作所必需的时间。
2、宽放时间:指作业员除正常工作时间之外必须的停顿及休息的时间。包括操作者个人事情引起的延迟,疲劳或无法避免的作业延迟等时间。对于没有规定发生时间、发生频率、所需时间的不规则要素作业,并不在正常时间范围之内,而属于宽放时间。
3、标准速度:没有过度体力和精神疲劳状态下,每天能连续工作,只要努力就容易达到标准作业成果的速度。
—2—
标准工时的界定条件
1、规定的环境条件下;
2、按照规定的作业方法;
3、使用规定的设备、治工具;
4、由受过训练的作业人员;
5、在不受外在不良影响的条件下;
6、达成一定的品质要求。
—3—
标准工时的作用
1、效率管理
效率是对标准时间达成程度的指数,标准时间决定之后,管理人员必须在标准时间内完成作业。
2、设备能力
机器设备具有多少能力,必须依据标准时间作计算分析,以作为设备购置之依据,及采取适当之应变措施。
3、设备计划
透过标准工时及设备的产能,将整厂的设备作最佳的安排。
4、人员及负荷计算
生产计划拟定后,可依据标准时间计算所需之人工小时及所需人员,而且前机器设备具有多少能力,期负荷的情况都需依据标准时间来计算。
5、标准产能计算的依据
依照各产品的标准工时,将每天的工作时间来计算各产品的标准产能。
6、生产计划进度安排
依照标准工时来安排各产品的生产进度。
7、日程管理
制造部门依据标准时间计算出应生产的产品数量,安排人员设备的配置、日程计划、生产管制等工作,以达成要求的数量。
8、人机配合的计算
依据标准时间,方可适当安排人员及机器的配置,以减少人力的浪费。
9、生产线平衡的计算
生产在线各工作站若配置不当,会造成瓶颈及过多空闲时间而造成浪费,需在标准时间适当地安排工作。
10、人员计划
将标准工时所计算出的产能来安排工作人员,在将全厂的人员来排定计划。
11、工作方法的改善
将各单元的标准时间予以计算出来,作为改善的参考依据,同时可作为改善前后的比较。
12、作业指导训练的标准
在现场生产单位的作业指导训练中,标准工时是其各作业单元效率的依据。
13、工作绩效评估及奖金计算
实施奖工制度必须籍由标准时间来衡量工作绩效,才能公平合理计算奖金。
14、新产品的开发
新产品的开发,可依据旧有产品单元标准时间来预估所需要的成本。
15、人工成本计算
标准时间为直接人工成本计算的基本数据。
16、订定产品价格的参考
标准工时可将产品一部份的成本计算出来,再加上其他因素,可作为产品价格的参考。
—4—
标准工时的构成
准时间=正常时间+宽放时间=观测时间*(1+熟练修正数+努力修正数)+观测时间*宽放率
A.正常时间包括主体作业时间和副作业时间:
主体作业时间:按照作业目的进行的作业。指能创造价值的作业,如改变产品外形,改变产品性能等。
副作业时间:与主体作业同步发生,起附属作用。如取放工具、检查等。
B.宽放时间:
私事宽放时间:作业过程中,满足生理要求的宽放时间,如上厕所,喝水,擦汗。
疲劳宽放时间:为了补偿工作过程中体力和精神疲劳,采取的休息或操作速度减弱的宽放时间。
特殊宽放:学习宽放、机械干涉宽放、奖励宽放、工厂宽放、其它宽放。
作业宽放时间:补偿作业过程中发生不规则的要素作业。如用处理不良品等。
集体宽放时间:集体作业时,对于个体差异产生损失的补偿。如熟练度的差异,工位编排产生的损失等。
宽放系数表
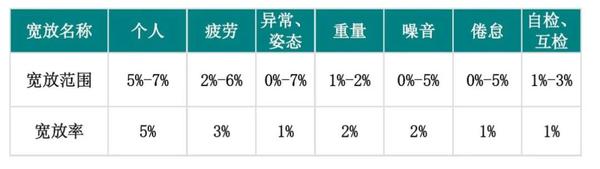
注:宽放种类很多。但在实际计算标准工时时。不能将所有宽放都考虑在内。因宽放越多说明作业效率越低。一般宽放效率10%-20%之间均为正常尺度。根据公司产品特点总宽放率设置为10%-20%。总宽放率=Σ+各宽放率=15%
—5—
标准工时的评比
作业观测者(时间研究者)把的标准化作业状态(速度、动作等)和观测对象(操作者)的作业状态相比较,使之定量化。
平准化法(平准化法又称西屋法)
熟练程度(表现工人的工作能力,在完成工序连续性,动作有没有犹豫不决情况)
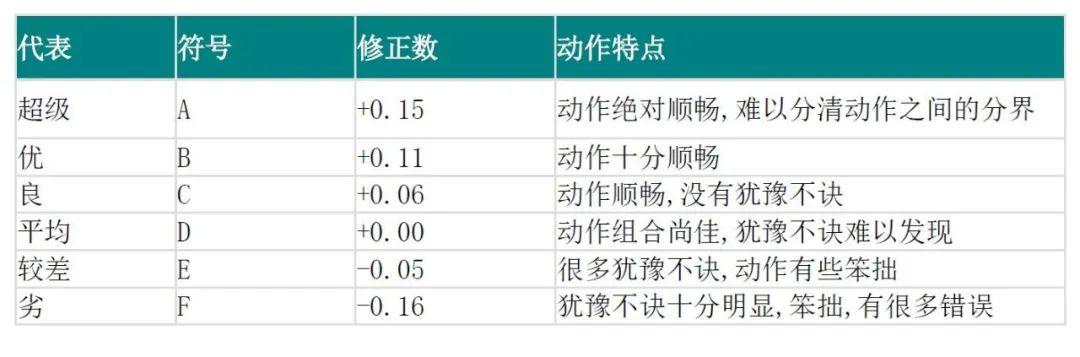
努力程度(表现在动作的速度上,工作的重要会影响速度,而工作时集中注意力亦影响速度)
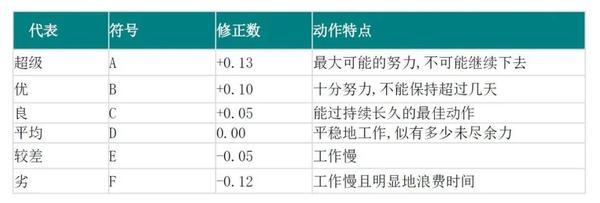
—6—
标准工时四种计算方法
A、秒表法
优点:应该可以说这是四种方法中最简单快速、实施成本最低的方法。
缺点:假若操作单元时间都非常短,那么测量的人员也是反应不过来的,这样数据就产生了问题。另外,此方法缺少二次分析、追溯的能力,因为记录下来的仅仅只有一个数字而已。
建议使用场合:量产阶段。一般可以用来测量每个工位周期时间,绘制线平衡图表,可进行人机作业分析。由于测量精度问题,不建议测量周期时间较短的工位,不建议将数据进行双手作业分析,不建议据此生成标准资料。
B、影像法(视频法)
优点:这种方法是我见过使用率最高的方法。它的精度相较于秒表法会更高,由于视频的存档,它具备二次分析、追溯的能力。
缺点:但是它的问题就是分析的低效:很多公司使用视频剪辑软件对视频进行分割,从而获取操作单元时间。因为不是专门的分析软件,所以整个分析过程痛苦无比,费时费力。
建议使用场合:量产阶段。几乎可以运用所有的场合。注意精度需求和分析精度之间的权衡。
C、预定工时法
优点:具体的方法有:MTM,MOST,MOD。它们最大的优点就是不需要实际生产。另外,预定工时法的分析结果可以作为一个改善的基准。比如,工程师在规划阶段分配了一个手腕动作的时间,但在具体实施的时候发现工人使用了一个手肘动作去完成。那么是不是现场的布局有问题,需要把物料放在手腕能够取的范围内呢?
缺点:必须对每个编码的起始点,结束点,包含动作了如指掌。否则很可能产生遗漏了某个工作导致预定工时分析出来的工时偏短。另外,如果长期使用预定工时法会导致疏离工厂现场,导致分析结果脱离实际。
建议使用场合:新产品导入阶段、量产阶段。注意根据不同的周期时间选择不同级别的编码,不建议高等级动作采用低等级编码分析。注意编码假设环境与现实环境是否相同。
D、标准资料法
优点:能利用企业历史信息进行快速制定标准工时。并且由于是企业本身产生的历史数据,所以标准工时更加准确,同时,通过该历史数据中设定改善目标,也更加具备可实施性。
缺点:标准资料库的形成不是一朝一夕就能形成的,需要企业不断地从上述几种测量方法中总结提取,形成标准资料库。这个过程就像没有尽头的马拉松一样,因为总是有新产品出现,新工艺出现,需要不断的补充改善,岂是一般的企业能坚持的了的?
建议使用场合:新产品导入阶段、量产阶段。几乎可以运用所有的场合。注意历史数据所在环境与现在数据所在环境是否相同。
—7—
秒表设定法典型步骤
1、准备秒表、笔和记录窗体《现场观测工时统计表》。
2、选择运作顺畅生产线,记录每道工序的工序名称和观测后用秒表测试的操作时间。其中,每道工序观测后的操作时间最少记录5组数据;可便于计算出标准工时,并能够挑选出更合理的数据。
3、在观测的同时必须对每道工序进行宽放和评估努力,熟练程度;并在过程记录窗体上作记录。对人员的配置同样做记录。
4、产品加工的流程图务必在过程记录窗体上体现,便于清楚知道产品加工的顺序和正确性。
5、在加工过程中,影响作业时间的工治具,辅具必须在过程记录窗体上体现。
6、计算出每道工序的标准工时,找出瓶径工时,并计算出产线时产和人均时产以及线平衡率。
—8—
标准工时变更
1、新增机型投入生产时,必须建立相应的标准时间。
2、工程变动、工艺变更等引起作业情况变化,必须对相应的标准间做相应更新。
3、工治具的增加引起的工序操作的变动,必须对相应的标准时间做相应更新。
4、新产品和更新过的产品标准工时由IE工程师建立。
由于作业人员流动过于频繁,新进员工操作生疏,厂房内温度过高,通风设施不够好;作业过程中经常出现少料,缺料和混料现象,作业方法不当,工作顺序的复杂化,引起异常工时增加。