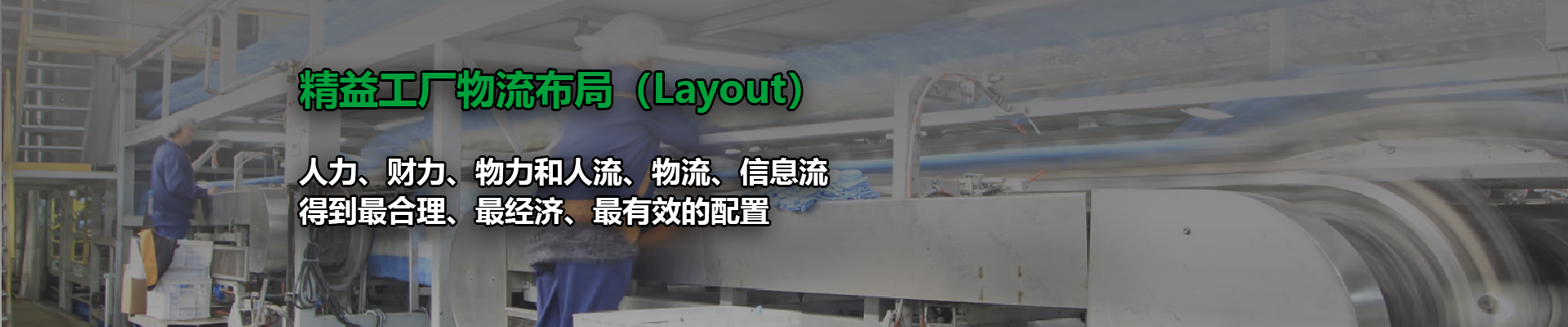
什么是精益布局
精益布局的目标是使作业流程中的浪费和过载最小化,同时增强现场的目视沟通。 传统布局结构没有考虑到生产制造过程中的工艺路线的紧密程度和生产组织过程中的流动要求,严重制约着企业精益物流的运行和精益制造模式的建立, 对企业生产制造现场的管理带来了很大的难度,现场混乱不堪、物流资源耗费巨大、场地拥挤无序等现象严重阻碍了“单件流”的实现,整个制造周期由于传统的布局结构而无法得到有效改善。
精益布局的优势:
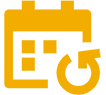
降低生产周期时间
快速响应客户
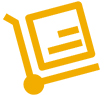
降低库存、消除搬运
有效减少浪费
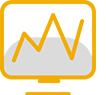
提高设备整体产出能力
提升OEE指标
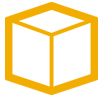
提高生产空间利用率
通畅便捷的物流
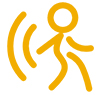
优化不必要的浪费
减少作业量
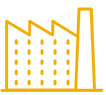
营造舒适的工作环境
改善作业环境
精益布局要注意什么
布局规划
- 流畅原则:各工序的有机结合,相关联工序集中放置原则,流水化布局原则。
- 最短距离原则:尽量减少搬运,流程不可以交叉,直线运行。
- 平衡原则:工站之间资源配置,速率配置尽量平衡。
- 固定循环原则:尽量减少诸如搬运,传递这种Non-Value Added的活动。
- 经济产量原则:适应最小批量生产的情形,尽可能利用空间,减少地面放置原则。
- 柔韧性的原则:对未来变化具有充分应变力,方案有弹性。小批量多种类,优先考虑“U”型线布局、环型布局等。
- 防错的原则:生产布局要尽可能充分的考虑这项原则,第一步先从硬件布局上预防错误,减少生产上的损失。
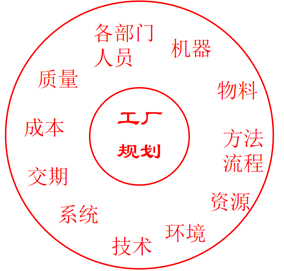
布局规划的要点
- 标准作业:减少作业中的浪费,设计时定义作业标准,避免盲目
- 物流顺畅:先进先出,最短距离,减少工序之间的在制品
- 信息流畅:便于信息传递,减少因信息不畅导致的停滞,便于以最少的管理人员管理整块区域
- 少人化:最优的人力配置,不能再少才好,优化工序
- 质量保证:布局规划的重点,及时发现不良品,以质量保证为目标
- 便于维护:要充分考虑到后期实际运行中的各类异常及变动,也就是考虑柔性
- 安全性:工厂一切活动都是以安全为前提
- 整体布置协调:各模块/区域实现均衡,不产生堆积或停滞,不拥挤,不空旷
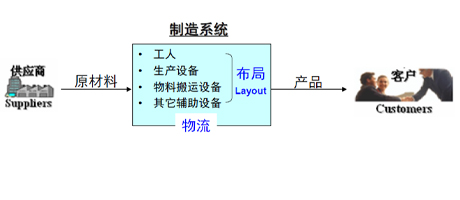
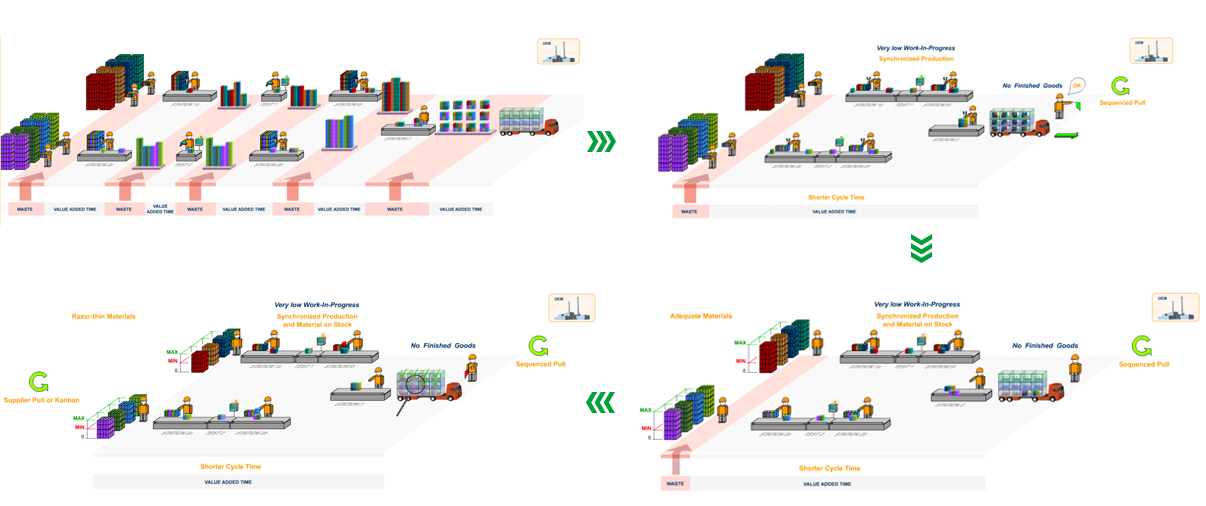
精益布局对未来有什么帮助
- 可视化
- 1、便于沟通管理信息流通
- 2、精益生产减少浪费
- 精益化
- 绿色化
- 3、符合人因工厂设计
- 4、便于数据采集工具导入
- 数字化
- 自动化
- 5、便于自动化导入
- 6、便于信息化导入导入
- 信息化
对未来的工厂建设发展埋下伏笔,规划好后续的措施,对企业发展战略和产能规划预想充足,整体物流规划、设备调试和安装、周转期周转量、产线布局及过程设计等因素,规划好新工厂在投产后避免出现产距长、设备不足或利用率低、工序不平衡等浪费。
总体目标是使人力、财力、物力和人流、物流、信息流得到最合理、最经济、最有效的配置和安排,即要确保规划的企业能以最小的投入获取最大的效益。
精益布局如何实施

- 基本状况把握:了解企业发展的基本状况和行业市场预测分析。
- 解读企业文化:解读企业文化,调阅企业视觉形象识别文件等文件。
- 价值流分析:进行工厂价值流分析(信息流、物流、工艺流程)。
- 绘制流程资源关系矩阵:识别流程和资源匹配关键点,重点控制。
- 产能规划:了解产能需求和客户需求节拍,平衡设备和人员能力。
- 确定主体布局规划。
- 规划设计说明:提供和布局规划设计总揽图、设备统计、面积、人员配置、工装夹具等资料,并作说明。
- 模拟和改善:采用三维软件或者模型、沙盘进行物流、搬运测试,不断完善布局规划设计内容。
- 规划执行训练:新工厂搬迁,根据规划实施训练和说明,确保方案的落实和执行。
- 搬迁后跟进:新工厂投产顺利后,对规划进行跟进和回访,了解不完善点,提出改善建议。
精益布局相关案例
-
- 一个流的生产布局
-
- U型线布局
-
- 精益物流布局
-
- 看板拉动布局