1.定义:
工厂中人或设备处于等待(含临时性闲置、停止、无事可做等)状态造成的资源浪费,被称为等待的浪费。
2.等待浪费的分类。
(1)来料不及时造成整体浪费。
当上游制程无料可供时,那么不管整个生产链中各制程平衡与否,换线与否,人机安定与否……都会出现同一状况--等待,人和机都在等待。
(2)生产不平衡造成非瓶颈处的局部等待。
第一种情况:当下游的产能小于上游产能时,会在下游制程前出现WIP,同时上游制程在一定时候需要停下来等待,这种情况是产能不平衡等待最常见的一种。
第二种情况:和上面情况相反,上游产能小于下游产能,为了平衡一定时间内上下两制程的产出,完成生产计划同时消除库存,需要下游作出等待。
如果按照正常班次:
PTH日产量1920pce/16Hr,SMT日产量1360pce/16Hr,这样安排的话,PTH制程上班的16个小时中有4.6个小时人和机处于等待状态。
(3)生产计划导致的等待。
第一种情况:制程间生产计划安排不合理,致使各制程产出不均衡。
第二种情况:P/O或W/O减少造成的整体性等待。
(4)生产线切换造成的等待。
换线换模时,人会产生等待,换线时间越长,等待时间越长。
(5)生产中设备原因
(含设备故障、设备调校、设备非标准速度运转等)造成的下游制程等待。
(6)人机不平衡造成的人或机器的等待。
人机不平衡造成等待,或者人等机或者机等人,但到底需要人等机还是机等人是个经济问题。如人每小时需要付给他20元,机器连同机器相关的场地水电只支出10元,那么肯定让机器歇着等人合算,比如电脑。但在企业里大多数情况下是机器单位支出肯定比人的支出贵得多,所以人机不平衡解决的第一个问题是消除机等人的情况。
第二种情况就是解决人本身等待的问题。
举例:T公司铣削制程有4台机器,每台机器l个人,分别每人看1台,作业流程分别为:
①人取产品,装夹产品(10秒)。
②机器作业,人等待(60秒)。
③人取产品,装夹产品(l0秒),然后依次循环。
则周期时间10+10=70秒,人的利用率为10/70=14.3%,机器利用率60/7O=85.7%。在此案例中,机器作业时间远长于人作业时间,造成人等待和利用率只有14%。见图1。
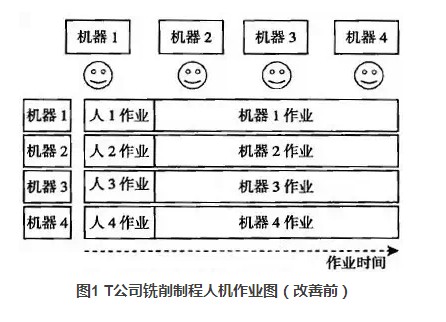
图1 T公司铣削制程人机作业图(改善前)
(7)品质问题造成的停机等待。
生产中良率不会是100%,但稳定的生产中品质是可控的,变异很小的,是可以在生产计划时预见的。而造成停机等待的品质问题指的是突然的批量性的问题,这时会造成生产的混乱,会安排重新生产、修机修模、返工、工程重新验证、找客户签样板等。这个问题导致的等待和来料原因导致的等待有相似之处,就是比较突然,非连续性和可预见性,通常在这时人和机就在等待。
(8)最小搬运量定额太高,搬运批次少。
(9)管理造成的人、机等待(如安排不当、开会、操作不熟练等)。
3.等待浪费的影响。
(1)延长L/T。等待对生产周期有直接的影响。等待的累计时间越长,产品的生产周期自然就越长。
(2)成本压力增加。机器及人力闲置直接导致成本中固定成本部分的平均摊销变大,增加了成本压力。
4.等待浪费的消除方法。
(1)平衡产能。
第一种情况:利用生产线平衡法、制程间产能平衡法对生产线/制程进行平衡分析。
改善前有A-F共6个工站(制程),生产线不平衡,平衡率只有82%,等待较多。而改善后减少了一个工站,只有A一E共5个工站(制程),同时平衡率96%,减少了很多等待。
第二种情况:在产能平衡中经常用到的,对于生产速度不同,标准工时差异大的制程通常采用机器数量调节与班(日)生产时间调节的方式。
按照这个方案,PTH依旧上两个班16小时,而SMT上三个班,23甚至24个小时,前后制程基本产能平均了,人和机都无须互相等待了。
第三种情况:用相对加工速度慢但变化弹性大,物流流量小但频次高的cell模式安排生产。在cell模式生产方式下,各制程根据自己的生产需求安排人力设备,生产节拍是可变的,当等待出现的时候,现场管理人员会马上调整生产节拍,所以Cell生产模式也可以很有效地减少等待的浪费。
第四种情况:是最高级境界,即生产同期化,就是将上下游制程的生产节拍、生产能力和生产时间相同。在这时等待自然不会发生了,浪费也就消除了。
(2)减少搬运批量。
减少搬运批量,提高搬运频次是降低WIP的方法之一。大家知道,降低WIP是企业管理的一个重要指标,假如在满足这个指标后,WIP少了,只有1个小时,但你的搬运批量还是2个小时一次,那当有换型发生时,下一制程起码要等2小时,但如果你15分钟搬运一次,那么下一制程只需要等15分钟就可以了,所以减少搬运批量,提高搬运频次也是减少等待的有效方法之一。
(3)减少来料、生产计划、设备故障、品质异常等原因的停线。
加强物料管理能力,按需、按时供料;实施全员生产性维护(TPM),加强生产线自动化水平及设备保养维护,是减少等待的有效的但系统性强的方法。
(4)缩短切换时间。
导入快速换线(SMED)方法,消除/减少换线损失,可以有效地减少由于切换停机造成的下游等待,这点毫无疑问。
(5)人机平衡。
在人机联合作业中,我们需要考虑人与机的平衡,人机平衡就要尽量提升人与机的利用率。
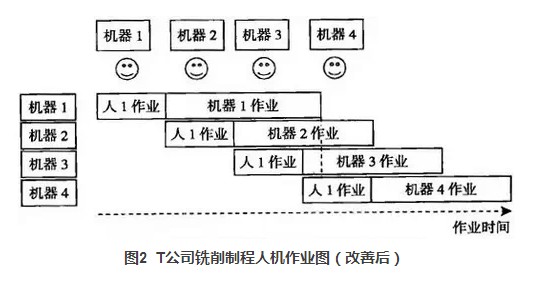
图2 T公司铣削制程人机作业图(改善后)
图2中,作业改为4台机器,总共1个人,作业流程分别为:
①人取机器1产品,装夹产品(10秒)+走到机器2(4秒),机器2/3/4运行。
②人取机器2产品,装夹产品(10秒)+走到机器3(4秒)。机器1/3/4运行。
③人取机器3产品,装夹产品(10秒)+走到机器4(4秒),机器1/2/4运行。
④人取机器4产品,装夹产品(10秒)+走到机器1(8秒),机器1/2/3运行。
依次循环。则周期时间70秒,机器运转60秒,人作业60秒(人走动3x4+8=20秒,装夹10x4=40秒,即人员总计工作时间60秒),所以人和机器利用率都是60/70=85.7%。在此案例中,人及机器的利用率都有了很多提升,更重要的是将作业人员从4个人减少到1个人,还减少了人的等待。
(6)对于管理
人、机等待,我们需要做的是合理的工作安排,作业员培训及操作机能及作业熟练度的提升,产线基础管理水平的提升等。