01
5why分析法简介
所谓5why分析法,又称“丰田5问法”,起源于丰田公司的一次新闻发布会,有人问:丰田汽车的质量为什么会这么好?大田耐一如此回答:我碰到问题至少要问5个为什么。我喜欢在车间里停下向工人发问,我就只问一个问题“为什么”,直到他的回答让我明白、满意为止。——这就是著名的“5个为什么”的起源。
对一个问题点连续以5个“为什么”进行发问,以当前问题的结果作为下个问题的原因持续追问下去,直到查明其根本原因。
虽然被称为5个为什么分析法,但在实际运用中并不限定只做“5 次为什么的探讨”,主要的目的是找到根本原因为止,有时可能只要3次,有时也许要10次,正如成语“刨根究底”的意义一般,而不是一知半解、浅尝辄止。
5why分析法其实是一种诊断性技术,常被用来识别和说明因果关系链,它的根源会引起恰当的定义问题。
5why分析法的关键所在:鼓励解决问题的人要努力避开主观或自负的假设和逻辑陷阱,结合所学知识和累积的经验,从事件结果着手,沿着因果关系链条顺藤摸瓜,直至找出原有问题的根本原因。
02
5why 分析法的运用
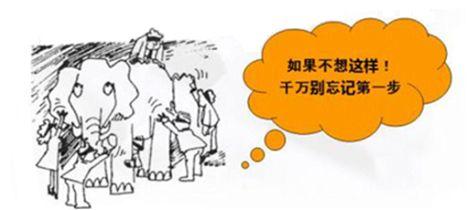
5why分析有助于解决零星的品质缺陷引发的问题。通常被用作一个解决实际问题过程的一部分,即根本原因分析和调查。
2.1 案例分析之前的准备
准确的认识问题,是解决问题的前提。千万别忽视第一步:要向有关人员清晰陈述所发生的问题和相关信息,做到让优化人员都了解要分析的问题是什么,及时是不熟悉该类问题的人。
通过发生问题(纷争)的现场与显示其状态的实物,可以了解到问题(纷争)的详细情况。
第一,通过现场、实物把握实际情况。要抓住问题发生的部位、地点、时间段、时间、发生频率、种类、类型、状态、比例等事实,在有条件的情况下可模拟情景再现。
第二,数据的掌握。整理历史统计数据,获取一定时期的统计数据作为案例分析的数值参考。
第三,了解问题部位的构造或原理。如果是结构性产品,最好能画出草图以便能进行直观分析;如果是原理性产品可以描绘工程略图进行流程和原理分析。
2.2 5why分析法的实施步骤
5why分析法的使用实施通常有三大步骤:把握现状、原因调查、问题纠正,如图1所示。
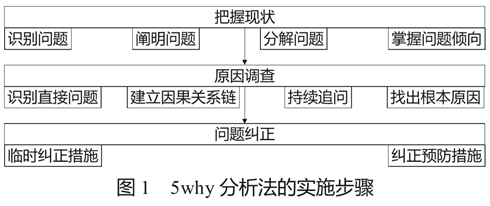
2.3 5why分析法的原则
当前国内许多企业都使用5why分析法对质量问题进行分析,也制定了各式各样的纠正预防措施,用来防止同一问题再次发生,但却发现未取得预期的效果,
其关键原因在于分析的过程中并没有找到问题的根本原因,而造成此现象的一大原因是没有正确使用5why分析法。通过长期实践和持续改进,本文归纳了5why分析法的10个原则。
第一,“现象” 及“为什么”的主语只有1个,使用“XX做了XX”的简洁的句子来表达。
第二,在分析完所有的“为什么”之后,反过来阅读分析结果,确认论点是否合乎道理,是否出现思维跳跃。
第三,必须持有这样的观点,即这项“为什么”如果不发生的话,前一项“为什么”是否真的不会发生。另外,必须列举出所有并列关系的因素。
第四,在找到与防止再发生对策相关的因素之前,必须一直往下进行“为什么”分析。
第五,要特别注意避开牵强的“为什么”,否则将会偏离分析方向。
第六,避开对人心理方面的主观原因进行追究。
第七,要用词精确,避免使用“不好”、“不够”、“不到位”等类似的词语。
第八,在同一个原因里不能同时描述原因和结果。
第九,对于作为标准的东西以及事物也应使用“为什么”进行推究。
第十,认真地验证现场以及实物,应把焦点放在致使该现象产生的内容上,并依据发生的原理/原则(或者是不会导致该现象产生的原理/原则)来进行分析。
03
应用案例
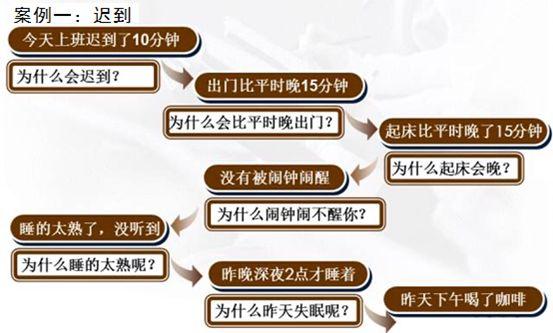
案例二:使用POP铆钉铆接的散热板在运行过程中掉落的5why分析。
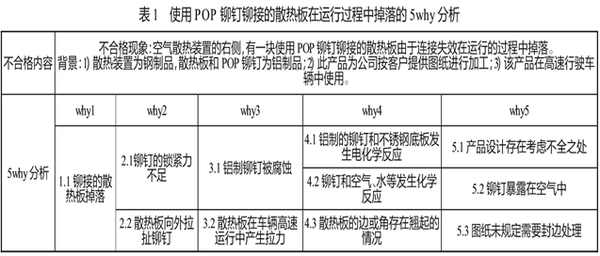
经确认,why5.1 和why5.3 已经属于最根本原因,故可以停止往下分析,但由于5.2所描述的原因还不是最根本的原因,故需要接着分析,如表 2所示。
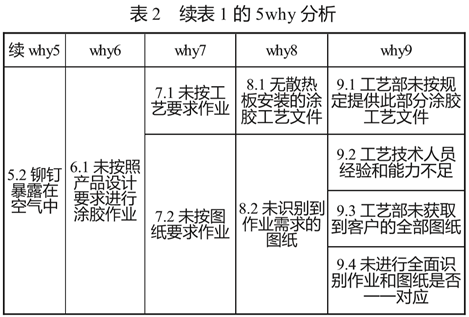
针对事故的现象制定了应急措施和防止再发生措施,如表3所示。
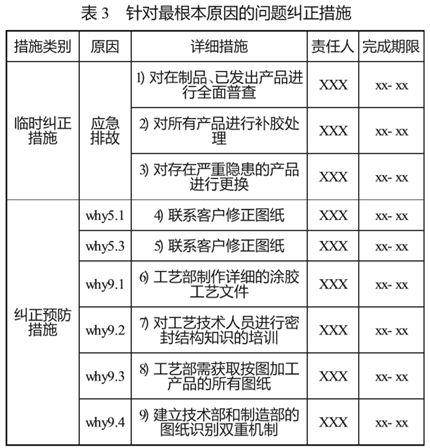
04
结论
作为企业中最常用的质量分析工具,5why分析法在防止产品质量问题再次发生上取得了卓越成效。经过实践证明,只要正确使用了5why分析法对问题进行分析,找到根本原因,制定了有效的整改措施并正确实施,可以有效防止问题再次发生。