一、疲劳分析背景
在日益严酷的市场竞争中,产品的寿命和可靠性成为人们越来越关注的焦点。每年因结构疲劳大量产品在其有效寿命期内报废,由于疲劳破坏而造成的恶性事故也时有出现。
据统计,每年早期断裂造成的损失达$1190亿美元,其中95%是由于疲劳引起的断裂。应用疲劳耐久性技术,其中的50%是可以避免的,因此许多企业将疲劳耐久性定为产品质量控制的重要指标。
在传统的设计过程中,机械产品的疲劳寿命通常是通过一定量物理样机的耐久试验得到,不但试验周期长、耗资巨大,而且许多相关参数与失效的定量关系也不可能在试验中得出,试验结论还可能受许多偶然因素的影响。
产品投放市场后,耐久性问题的出现造成许多新产品失去竞争力,给企业带来巨大的经济损失,同时又使企业形象蒙受巨大的负面影响。在中国,疲劳耐久性与可靠性问题更是普遍存在,是国产产品缺乏国际竞争力的最重要因素之一。
随着计算机技术发展而诞生的现代设计技术,使企业以较低的成本设计出高耐久性产品成为可能。在产品设计阶段采用ANSYS-SAFE,可在物理样机制造之前进行疲劳分析和优化设计,预测产品的寿命,真正实现等寿命周期设计,并可极大地降低制造物理样机和进行耐久性试验所带来的巨额研发费用。
二、疲劳的基本概念
1
疲劳的定义
当材料或结构受到多次重复变化的载荷作用后,应力值虽然始终没有超过材料的强度极限,甚至比弹性极限还低的情况下就可能发生破坏。这种在交变载荷作用下材料或结构的破坏现象,就叫做疲劳破坏。
2
疲劳破坏的特征
材料力学是根据静力试验来确定材料的机械性能(比如弹性极限、屈服极限、强度极限)的,这些机械性能没有充分反映材料在交变载荷作用下的特性。因此,在交变载荷作用下工作的零件和构件,如果还是按静载荷去设计,在使用过程中往往就会发生突如其来的破坏。
疲劳破坏与传统的静力破坏有着许多明显的本质区别:
1、静力破坏是一次最大载荷作用下的破坏;疲劳破坏是多次反复载荷作用下产生的破坏,它不是短期内发生的。
2、当静应力小于屈服极限或强度极限时,不会发生静力破坏;而交变应力在远小于静强度极限,甚至小于屈服极限的情况下,疲劳破坏就可能发生。
3、静力破坏通常有明显的塑性变形产生;疲劳破坏通常没有外在宏观的显著塑性变形迹象,即便是塑性良好的金属也这样,就象脆性破坏一样,事先不易觉察出来,这表明疲劳破坏具有更大的危险性。
4、在静力破坏的断口上,通常只呈现粗粒状或纤维状特征;而在疲劳破坏的断口上,总是呈现两个区域特征,一部分是平滑的,另一部分是粗粒状或纤维状。因为疲劳破坏时,首先在某一点产生微小的裂纹,其起点叫“疲劳源”,裂纹从疲劳源开始,逐渐向四周扩展。由于反复变形,裂开的两个面时而挤紧,时而松开,这样反复摩擦,形成一个平滑区域。在交变载荷继续作用下,裂纹逐渐扩展,承载面积逐渐减少,当减少到材料或构件的静强度不足时,就会在某一载荷作用下突然断裂,其断裂面呈粗粒状或纤维状。
5、静力破坏的抗力主要取决于材料本身;而疲劳破坏的抗力与材料的组成、构件的形状或尺寸、表面状况、使用条件以及外界环境都有关系。
三、疲劳破坏基本知识
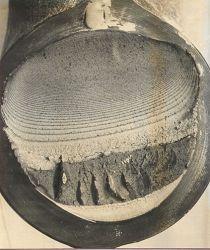
疲劳破坏的断口形状
1
疲劳失效的三个阶段
裂纹的产生、扩展和断裂三个阶段。其中裂纹产生阶段占了整个疲劳寿命的极大部分。
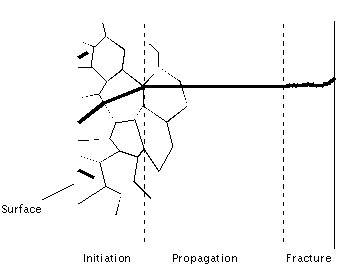
疲劳失效的三个阶段
2
疲劳载荷的简单描述
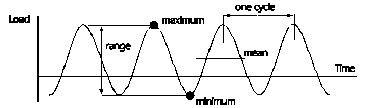
maximum load = Pmax
minimum load = Pminload range DP = Pmax - Pminload amplitude Pa = ΔP/2 (载荷振幅)(also called alternating load)mean load Pm = (Pmax+Pmin)/2load ratio R = (Pmax)/(Pmin) (载荷比 循环特征)amplitude ratio A = (Pa)/(Pm) (振幅比)
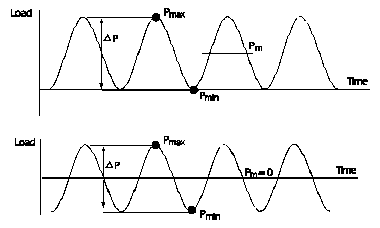
载荷比 R=0和 R=-1时的疲劳载荷
Zero based vs Fully reversed
3
耐久曲线
如对于钢,可能有10⁷个循环的耐久极限。表示无论经过多少次循环,只要应力幅值小于耐久极限应力,则将不会引起疲劳破坏。
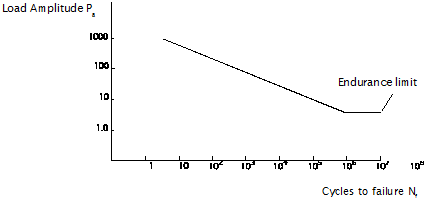
耐久曲线
(可对载荷幅值和循环次数都取常用对数log10)
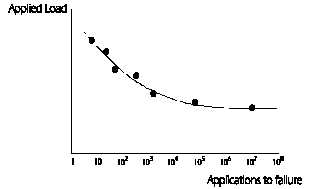
疲劳测试结果
四、疲劳数据的推广
对于特定部件的应力幅和耐久曲线的关系并不通用,当部件的形状改变后即无效。要使这个关系广泛使用,要在三个方面进行推广:
- 使常数幅值的耐久曲线用于分析复杂的载荷历程;
- 从光滑试件测得的耐久曲线用于不同形状的零件上;
- 从一种材料测得的耐久曲线用于计算另一种材料的疲劳寿命,并且如果可能的话,不用进行疲劳试验就可估算材料的疲劳特性。
1
复杂载荷分析
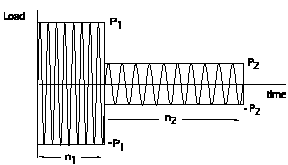
两部分常数幅值载荷组成的载荷历程
假设该载荷历程不断重复,直至零件破坏。实际的疲劳分析要求能计算承受各种不同幅值的复杂载荷的零件的疲劳寿命。
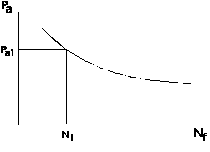
(a)
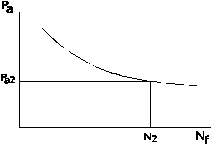
(b)
- 如果载荷只是由前页较大幅值Pa1 组成,可从耐久曲线图(a) 中得到,当循环次数n1 等于破坏时的循环次数N1时,零件发生破坏。显然,此时n1/N1=1。同理,如果载荷只是由前页较小幅值Pa2 组成,由图(b)有,破坏时n2/N2=1。
- 要计算组合载荷作用下的寿命。假设各种幅值的载荷单独作用,则当n/N=1时发生破坏。
- 对于两种载荷组合,则当n1/N1+n2/N2=1 时,零件发生破坏。
- 对于更加复杂的载荷,其中有多种不同的幅值,发生疲劳破坏的条件为:

实例:
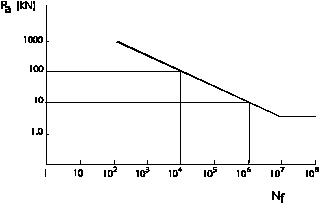
载荷组成:
- 10 cycles of a load amplitude 100 kN
- 2000 cycles of a load amplitude 10 kN
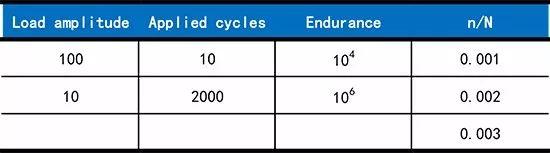
计算得总的Σ(n/N)=0.003。根据Miner’s 法则,当总和值Σ(n/N)=1时,将发生破坏。即当上述的载荷组合重复次数为333次时,将会发生破坏。因此计算的寿命也就为载荷历程重复333次。
2
平均应力的影响
平均应力会影响到疲劳寿命,对于同样的应力幅值,平均应力越高,疲劳寿命越短。因此疲劳分析中还必须进行平均应力修正。下图曲线表示了平均应力对疲劳寿命的影响。
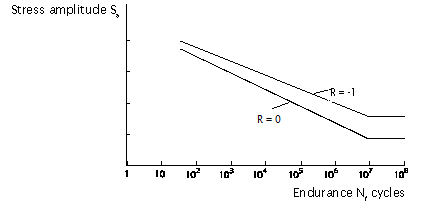
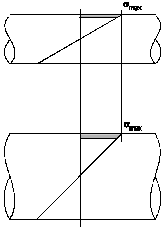
弯曲中测得的大、小试件在靠近表面处承受较大应力的材料的体积
由于疲劳裂纹的产生是表面现象,对构件表面的任何处理都会极大的影响到疲劳强度。这些重要因素包括:
- 表面质量:打磨、车加工、轧制 、铸造、锻压。
- 表面处理:电镀或包层。
- 由于装配过程或喷丸硬化、滚压等特殊处理引入的残余应力。
- 运用环境:腐蚀性气体、盐水腐蚀和使用温度。
- 接触面间的微振磨损。
五、疲劳分析基本方法
1
单轴应力寿命分析
用于分析单轴数据,应力幅用于计算疲劳寿命。单轴数据在实际问题中出现较少,通常推荐采用多轴算法。这种算法可通过S-N曲线和使用局部应变材料数据来完成,当使用局部应变材料数据时,疲劳寿命曲线由下式确定:
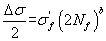
否则,寿命曲线由材料数据库中给定的SN值来确定。Goodman、Gerber或不进行平均应力修正在后面讲解。
2
单轴应变疲劳寿命算法
用于分析单轴数据,弹、塑性应变幅可用于计算疲劳寿命。单轴数据在实际问题中出现较少,我们通常推荐采用多轴算法。
- 真实的局部应力幅和耐久性之间的关系:
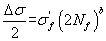
- 真实的局部应变幅和耐久性之间的关系:
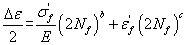
平均应力修正的三种等效寿命方程如下:
- Smith-Watson-Topper 平均应力修正:

- Morrow’s平均应力修正:
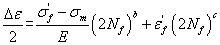
- 不进行平均应力修正:
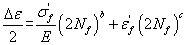
3
Goodman、Gerber平均应力修正
应力周期中:
- 应力范围 Smax-Smin
- 应力幅 (Smax-Smin)/2
- 平均应力 (Smax+Smin)/2
对于Goodman、Gerber平均应力修正,应力幅和平均应力用于计算平均应力为零时的等效应力幅Sa0和耐久性。下图为Goodman平均应力修正(参考DS理论部分):
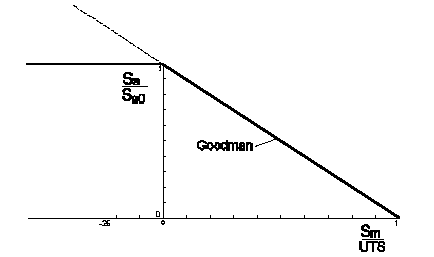
下图为Gerber平均应力修正:
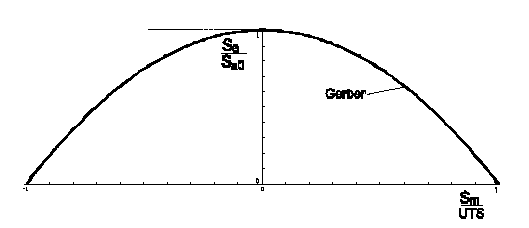
该方法允许Goodman、Gerber平均应力修正用于所有的耐久性分析。但两种方法对低周疲劳都不可靠。