IE起源于美国,但在日本得到了最深刻的践行、因此才导致了丰田生产方式TPS及“精益制造”LP的诞生。如今IE已经在全世界得到了认可与运用,成为消除浪费的“精益利器”
IE经过过年的专业研究与企业践行,已经取得了长足的发展,从实战的高度、广度、深度来看可以区分为基础阶段(生产单元改善)、提升阶段(生产方式革新)、深入阶段(VSM分析与全流程优化)。如果没有掌握VSM分析,企业的改善只能停留在点或线的范围,不能诊断与识别全流程端to端的浪费,也就无法全格局地实施流程优化。所以VSM不仅需要IE工程师牢牢掌握,更需要企业的各级人员、特别是中高层管理人员深刻理解并在实践活动中率先示范。不运用VSM,IE的精益改善始终有点“井底之蛙”之感
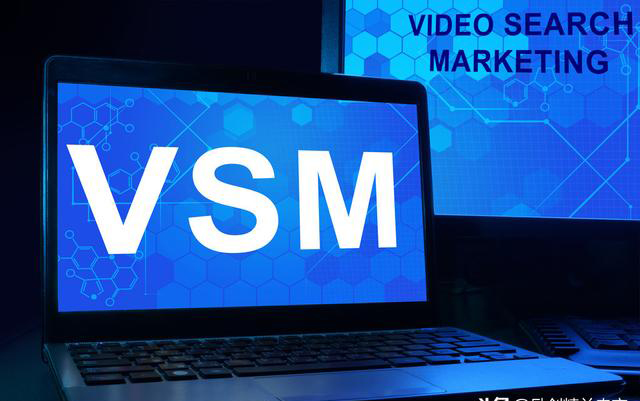
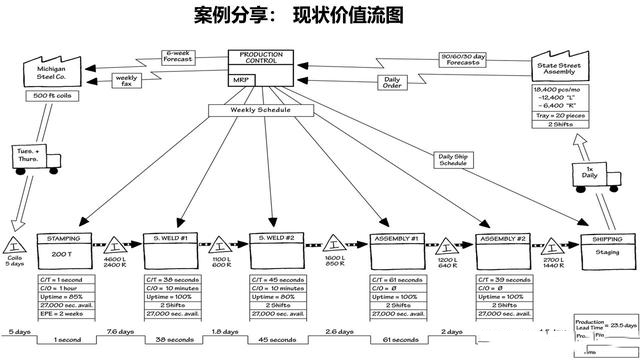
一、认知VSM价值流图 1、 价值流图VSM的起源 美国学者M.罗瑟与J.舒克教授在名著《学习观察》中首次提出了价值流图VSM的概念,并发表了著名宣言:哪里为客户提供产品与服务,哪里就有价值流,其间一定有浪费,挑战在于如何观察,找出浪费!
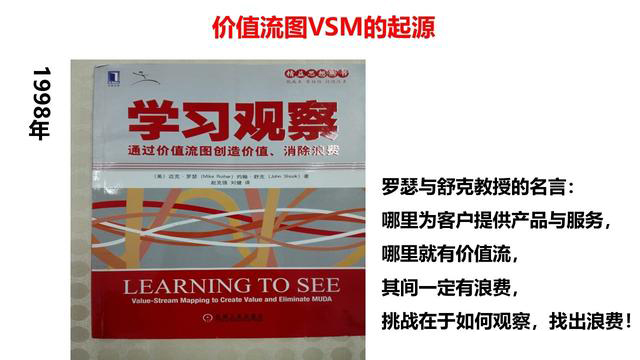
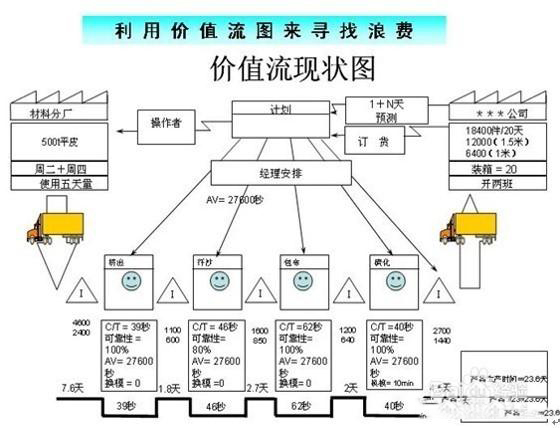
2、 价值流图VSM的内涵
价值流图(value stream mapping)是用一张纸、一支笔顺着物料和信息的流程收集关键数据,表示一件产品从订单到交付全过程(端to端),每一个工序的物料流和信息流的图表,并进行定量分析的工具
两大一级流程的数据收集与表达
- 产品实现的工艺物料流
- 订单实现的指令信息流
3、 价值流图VSM的用途
价值流图有助于全面、全过程观察和理解产品,通过价值流过程的物料流动和信息流动,特别是其中的增值和非增值(浪费)活动,从而发现浪费和确定需要改善的地方,更容易找出问题所在
价值流图还可以避免只应用个别的精益工具,进行局部、孤立的改善(工序IE改善、工艺PE改善)。通过绘制现状图,设计理想状态图并尽快付诸实施,通过这种方法,可以全面地改善价值流(点、面、流程全体),从而为客户、协作商和供应商带来最大的利益
4、 价值流图VSM的目标
价值流图是一种强力的可视化工具,它的主要目标是帮助我们确认运营流程中存在的潜在的(隐形的),对客户不增值的浪费活动
价值流图是任何企业展开流程分析的有效工具,既可作为企业内部沟通的工具,也可作为企业的战略规划工具
将企业流程所有相关的物流、信息流和现金流以图示的方式加以表达,有利于企业了解目标的经营现况和未来的经营现况
绘制一副现有系统的整体价值流程图,可以让所有人一致看出流程中的浪费情形, 未来面貌的的价值流程图可显示期望实现的未来远景,并有助于识别出价值流程中最能减少浪费情形的机会
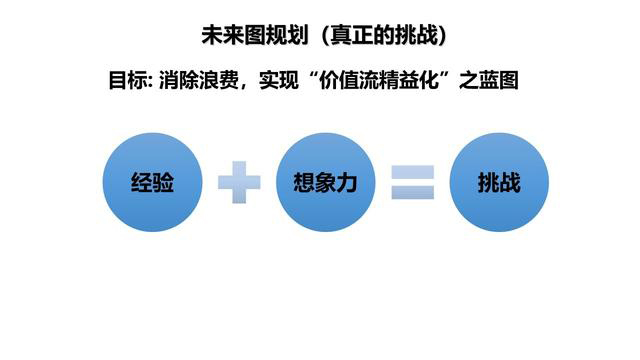
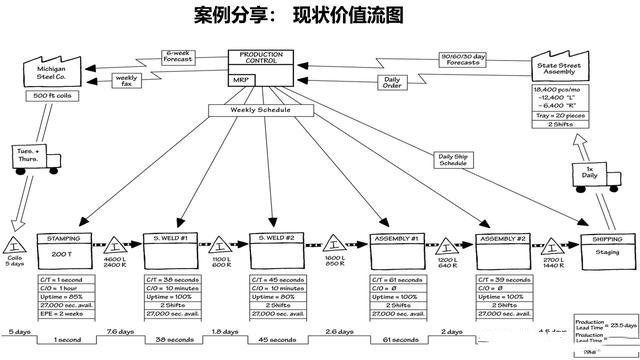
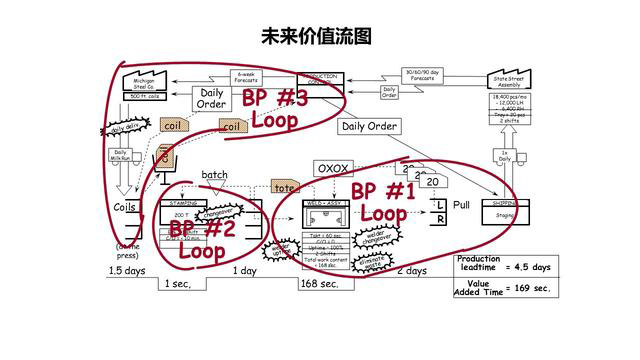
借助它,你可以找到最明显的5-10产生大量浪费的步骤,并开始着手制定消除浪费的计划并加以执行
二、绘制VSM价值流图
1、价值流图分为4个层别,可以从最简单的“点”(生产单元)入手、但有必要延伸至“线”(车间)及“面”(制造全流程),优秀的企业还将扩展至“链”(核心供应商以及核心销售商、代理商),被称为“价值链优化”
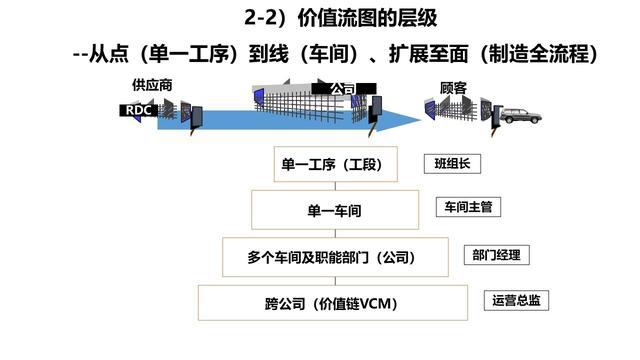
价值流图的层别进化
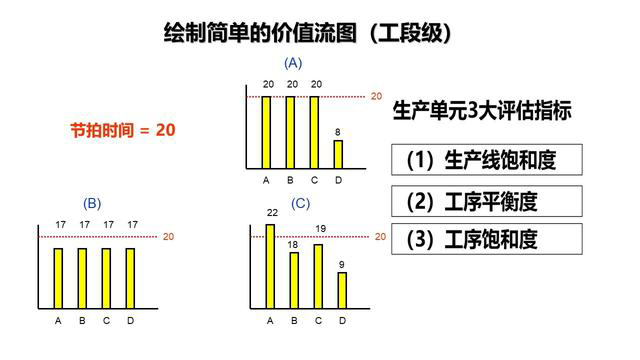
工段级VSM
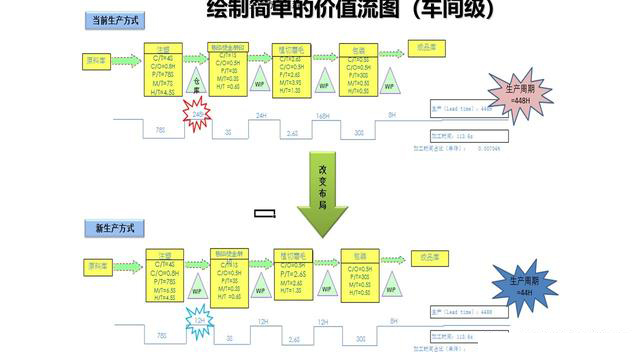
车间级VSM
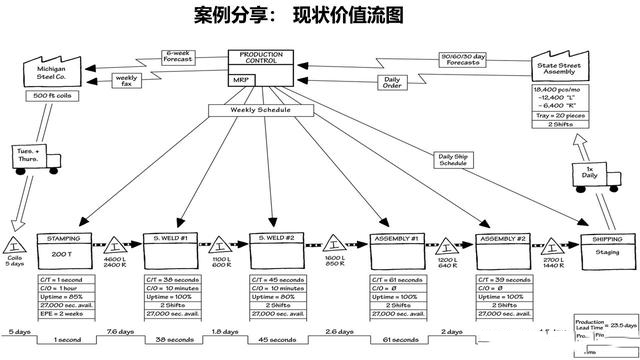
制造全流程VSM
2、绘制步骤
价值流图的基本特点
- 使用专用图标
- 2个流(物料流、信息流)
- 物料流:下半部分、从左到右
- 信息流:上半部分、从右到左
- 3层结构(部门、工段流程、时间线)
- 定量化数据
- 数据化评估
绘制第一层
- 画客户,供应商(协作商)和生产控制
- 输入客户需求(客户数据箱):客户原点,决定下游的节拍
- 计算每天的产量和包装箱需求
- 画出外向物流及其频率
- 画出内向物流及其频率
绘制第二层
- 从左到右添加工序(工段)框。有分叉流程时,使用并行排列
- 添加数据箱
- 添加信息流,标注其方式、内容和频率。“从右至左”、“从上至下”
- 搜集工艺属性并填写数据
- 标注操作工数量
- 添加库存位置、数量,并折算其周期时间
- 库存产生的原因不同,其折算周期时间的算法也不尽相同
- 画出推动,拉动,先进先出等物料流图标。“从左至右”
- 添加其它认为必要的信息
绘制第三层
- 增加工作时间
- 把VA及所有NVA时间对应到时间线上
- 计算工厂交付周期(L/T)和总增值时间(VCT)
三、运用VSM优化价值流
1、关键步骤一:价值流诊断与分析
价值流诊断与分析是建立在价值流图基础之上的有效分析工具,它起源于丰田公司的“材料及信息流分析”(MIFA)
任何的生产过程中均存在着材料流和信息流,价值流分析是从为客户创造价值的视角,将我们的注意力倾注于建立流动、消除非增值活动、快速增加价值的改善上去,并建立起材料流和信息流的联系
借助价值流图的价值流分析,是有效的”学会发现“的手段
- 定量计算与诊断现状流程中的“价值创造率”

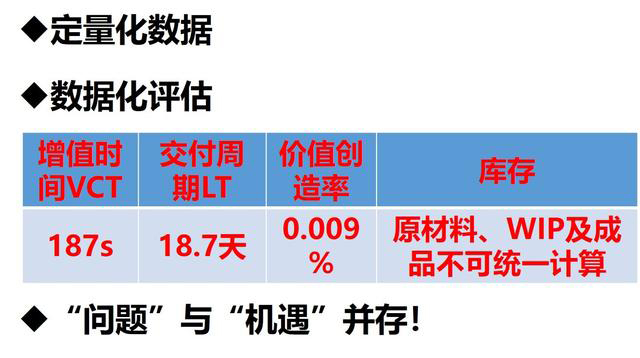
价值流分析用于观察和理解流程的现状同时绘制实施精益的未来蓝图,并定量评估流程优化后的“指标性提升”
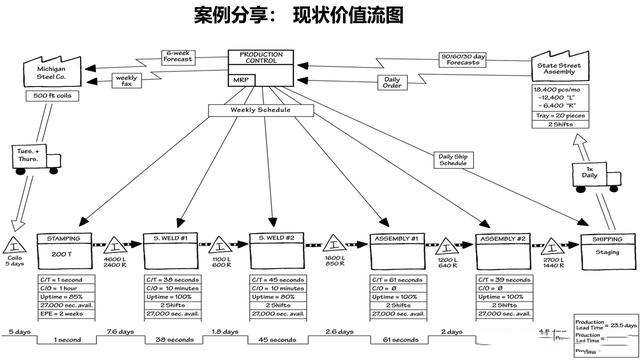
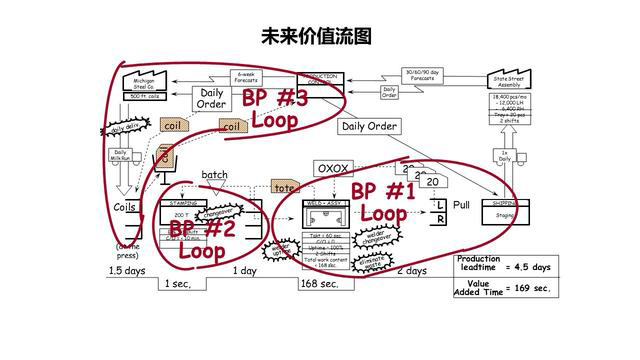
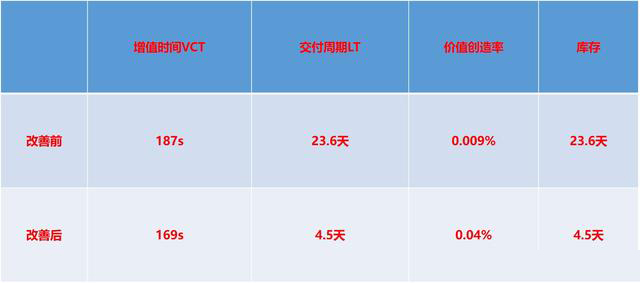
我们都可以发现,只要一切从客户的需要出发,积极运用企业内部及外部的各种资源,我们就能够发现、创造、传递更多的价值
客户价值流,就如同企业另一套贯穿内外的循环系统,为企业发展提供源源不断的能量,
精益的企业会将价值流分析扩展延伸到外部“供应商”及“协作商”(价值链管理VCM)
孤立地运行绘图是远远不够的,如果不能很好地理解精益生产的原则,那么绘制图形不会比早期和中期那些改进的工作车间更接近使浪费最小化并取得极好效果的目标
2、关键步骤二:价值流精益优化
精益优化思路一:杜绝过盈生产
过盈生产: 过多生产或过早生产
过盈生产会导致严重的后果
- 不必要的空间需求
- 额外的工时,搬运和分类
- 返工风险
- 库存风险
精益优化思路二:准时生产JIT
在当今“多品种、小批量、快交期、低库存、高品质”的市场与客户需求时代,未来不再是”大鱼吃小鱼“的规模竞争而是”快鱼吃慢鱼“的速度竞争,与时间的竞争成为企业的”第三极竞争力“。传统大批量制造模式已经成为企业竞争力的严重障碍,必须彻底革新!
而源于丰田的准时生产JIT理念正在以新的制造模式与科技革新浪潮引领着人类的制造业奔向“柔性灵敏制造”
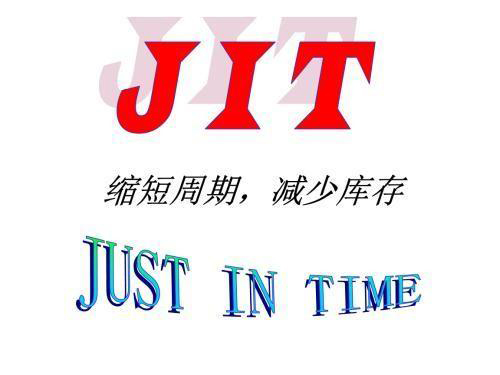
精益优化核心课题
“产品实现流程”的快速化
- 彻底革新“传统大批量制造模式“、导入”精益流动式制造模式“,大幅短缩制造周期Lead Time
- 大幅消除制造流程中的”等待“与”搬运“浪费
- 推行频繁、快速换型(SMED),实现全品种混流化生产Hybrid
- 制造全流程、各个工段之间实行“拉动式”
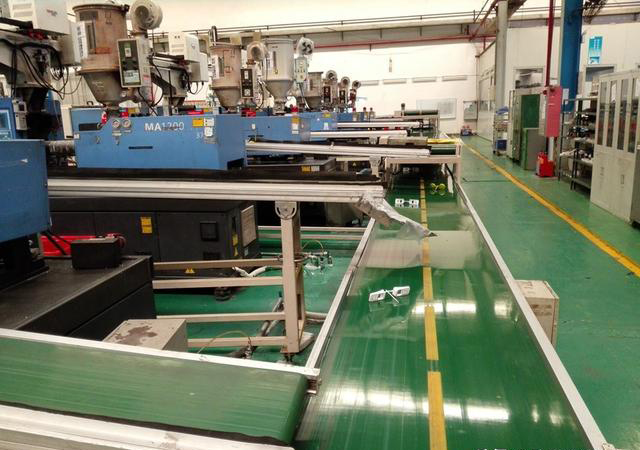
流动式单件流生产
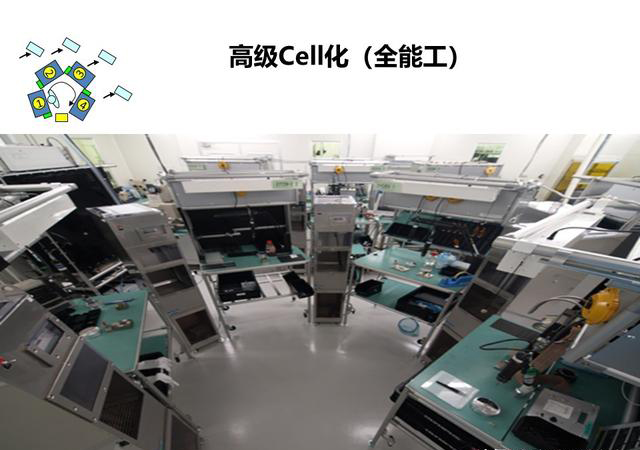
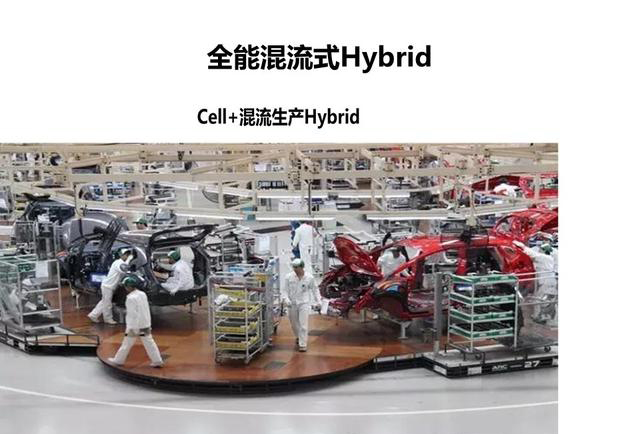
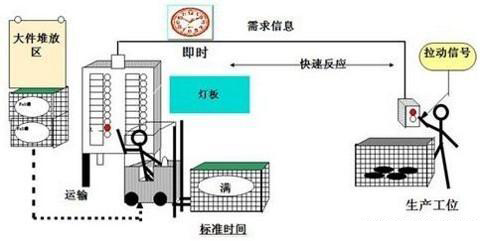
“订单实现流程”的准时化JIT
- 强化PMC职能的权威、提升PMC的价值存在
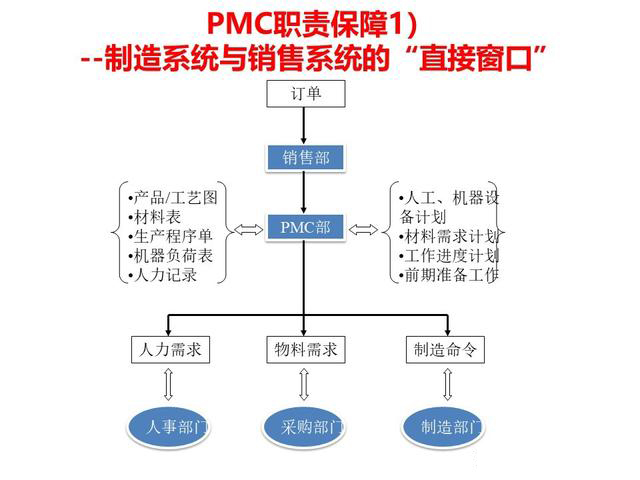
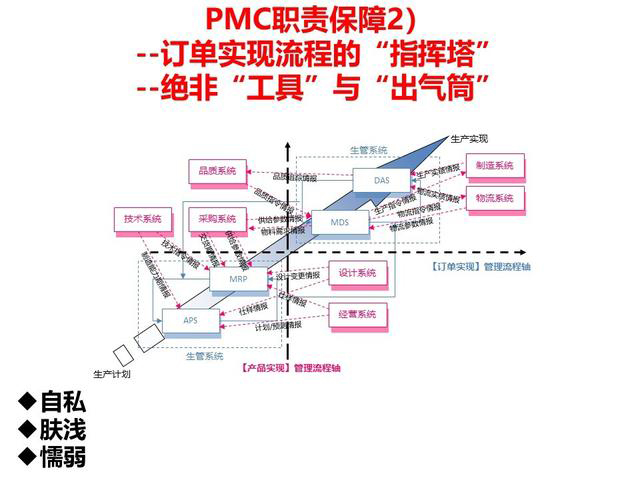
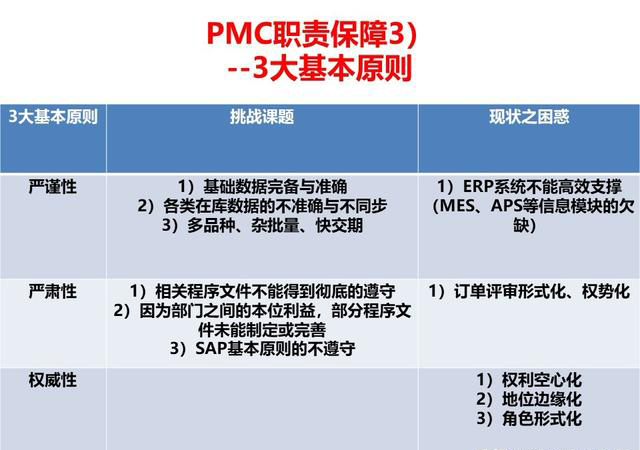
- 建立产、供、销联动的PSI计划体系
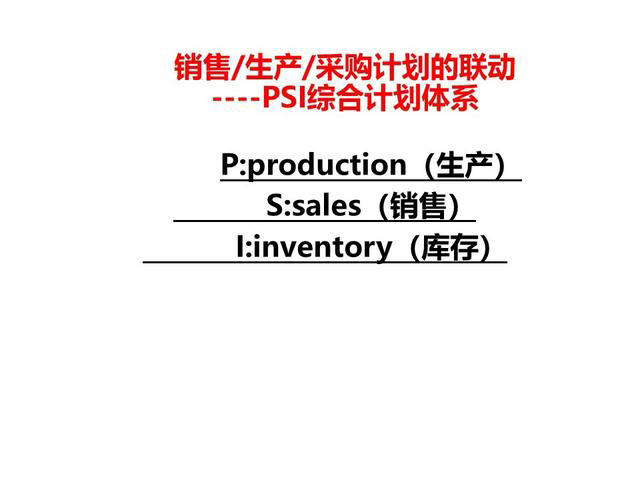
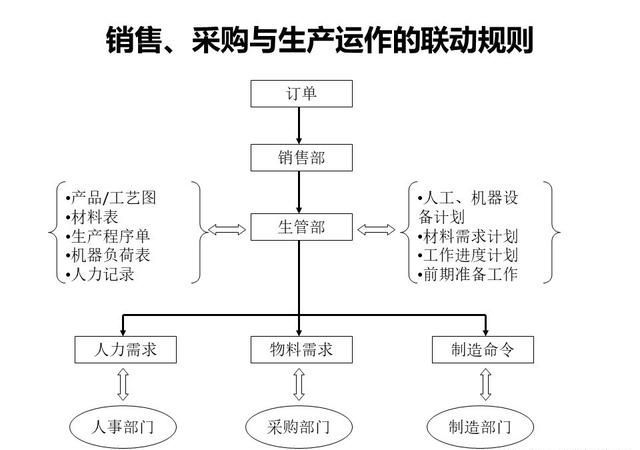
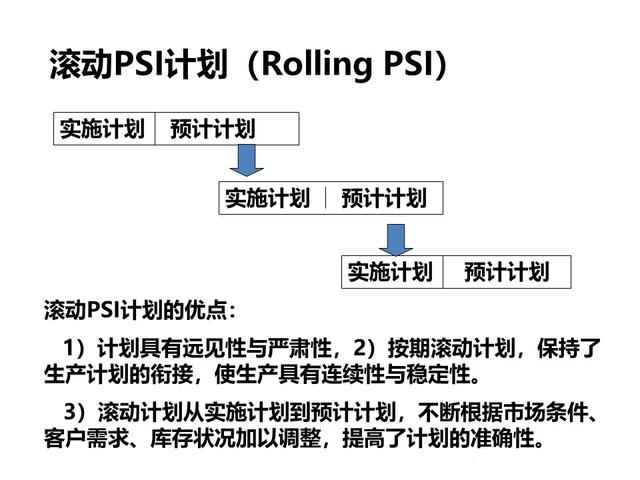
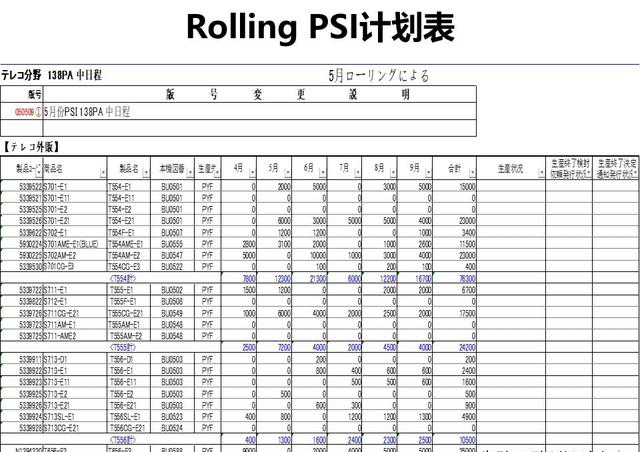
- 扩容ERP系统功能、导入MES与APS
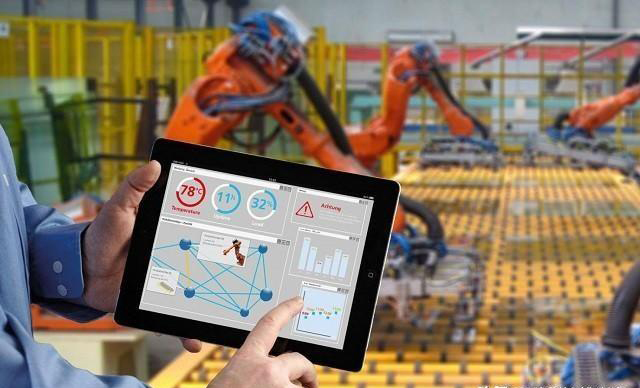
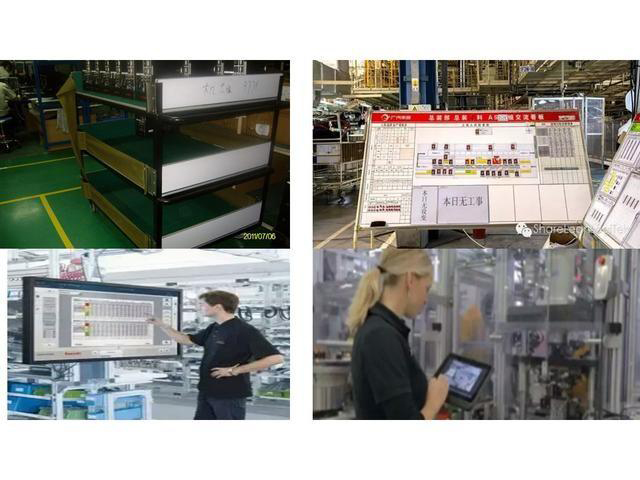
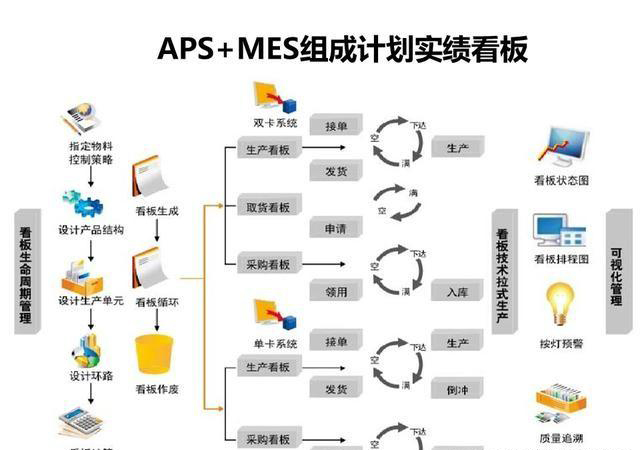

- 构建核心供应商的“战略联盟、互利共生“战略,运用VSM、JIT手段实现快速供货
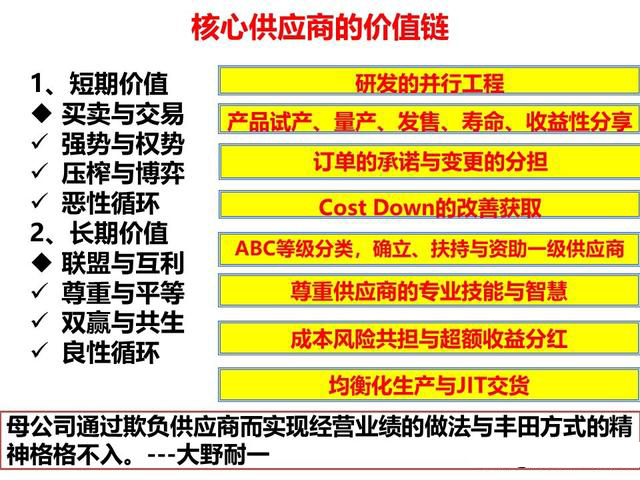