一、品种均衡的概念
品种均衡就是在一个单位期间内生产的产品组合平均化,使各种产品在不同单位期间不产生波动,在生产各种产品时所需前工序的零部件数量不产生波动。
在传统大批量的生产排程中,较常见的是以月为单位来安排生产。例如,某工厂某月有三种产品X、Y、Z需要生产。X产品的需求数为1000件,Y产品为600件,Z产品为400件。假若每月工作日20天,则传统生产计划安排为前10个工作日先将X产品生产完毕,然后6天生产Y产品,最后4天生产Z产品,如表4-1所示。这是一种常见的型态,也称为分段生产。虽然这种传统的大批量生产的方法可以节省作业转换时间,但是,与市场需求会出现很大的差异。因为一个企业的产品一般都有多个用户,每个用户对品种、型号、式样的要求不同,要求交货的具体时间也不相同。
企业应该在尽可能短的时间内(如1天)提供尽可能多的品种。而传统大批量的生产排程方法在某时势必使一部分产品供大于求,销售不出去,造成积压。同时,另一部分产品生产不出来,供不应求,发生缺货。无论是哪种情况都会造成损失和浪费。从表4-1可以看出,X产品通常会导致较长时间的库存,而Z产品却大半个月无货可供。
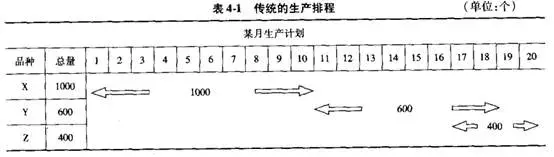
为了满足需求的多样性,可以进行如下改进:
可以减少生产批量,每天生产X产品50件,Y产品30件,Z产品20件,如表4-2所示。一个月20天每天重复1次,共20次,这样每天都可以生产出X产品、Y产品和Z产品,产品积压与短缺的情况将大大减少,企业内部生产资源利用率也大大提高。但是,此时(每天重复1次)作业切换次数为原生产安排(每月重复1次)的20倍,作业转换的辅助时间大大增加。为避免这种损失,就要设法减少每次作业转换时间。如果将作业转换时间降为传统方式的1/20,就可以弥补这种损失。
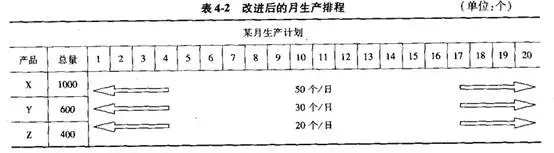
这种安排以天为单位,与传统的以月为单位的生产安排相比,其库存与满足市场需求方面都有较大改善。但是在每天的生产安排中,依然按照批量生产的方式,即先生产50件X产品,其次是30件Y产品,最后是20件Z产品,如表4-3所示。
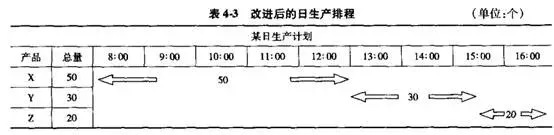
如果进一步细化生产单位,1天内产品X、Y、Z按照5:3:2的比例进行轮番生产,1/10个工作日重复1次,1天重复10次,1个月重复200次。这样,对顾客的服务与对企业资源的利用情况就会更好,不仅使得在更短的周期内产品种类出现的比率是均衡的,而且使在这些产品的生产中消耗的前工序的零部件数量尽量小地波动。

例如,X、Y、Z三种产品各由A、B、C三种零件组成,如表4-4所示。表4-5为X、Y、Z批量分别为50件、30件、20件时需要的各种零件数量。从表中可知,每日按照X、Y、Z各自批量生产,则各个零件波动较大。例如,当生产X产品时需要A零件为10个,当生产Y产品时需要A零件为2个,这样容易产生库存和人员的浪费。

如果1天内产品X、Y、Z按照5:3:2的比例进行轮番生产,1/10个工作日重复1次,则1/10个工作日内各个零部件的消耗速率就相同,如表4-6所示。
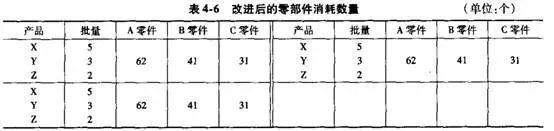
以这样的思路改进下去,不断细化生产单位,直到可以按照“X-Y-X-Z-X-Y-X-Z-X-Y”的顺序重复生产,达到最小的观察时间单位,满足精益生产倡导的以小时、分钟为单位进行安排的要求,实现均衡化生产。
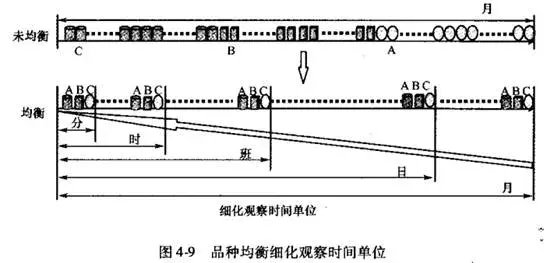
因此,按品种均衡就是要在一定的周期内各品种出现的比率是均等的,并且时间周期尽量缩短,尽量细化观察标准,如图4-9所示。这样使产品瞬时生产数量波动尽可能控制到最小程度。图4-10为按不同时间单位均衡的实例。
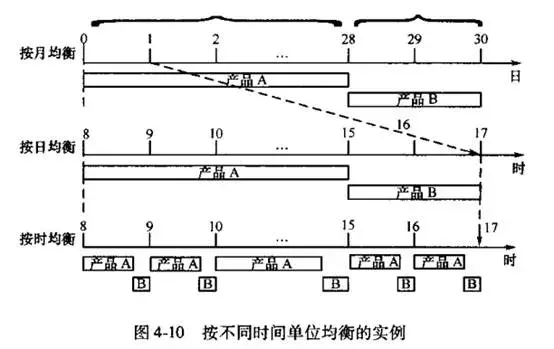
二、品种均衡的作用
从企业内部组织来看,由于面临多品种生产,企业必须配备多种设备和多种技能工,准备多种原材料。如果生产不均衡在一段时间内只生产一种产品,就会造成忙闲不均,在生产某一种产品时,可能一部分车间和设备超负荷运行,部分工人加班加点,某些原材料和外购件一时供应不上;相反,另一部分车间和设备负荷不足,甚至空闲,工人无事可做,某些原材料和外购件出现积压。其结果导致了库存的浪费和等待的浪费。
案例一:某汽车装配线装配A、B两种车型,装配顺序是4个A型车和4个B型车循环。装配线和部件线的生产节拍都是4min,生产部件A和B的工序都需要两名操作工。由于车型的不同而需要不同的部件,即装配A型车需要用到A部件,装配B型车需要用到B部件,如图4-11所示。
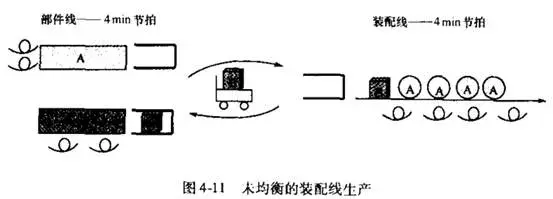
(1)如果按照准时化的要求进行生产,当后工序装配线装配B型车时,需要使用B部件,则生产A部件的生产线等待,反之亦然,这样就造成了等待的浪费。
(2)部件线的生产节拍仍为4min,如果为了使各工序不等待,就会出现生产过剩而库存增加,造成生产过早的浪费和库存的浪费,如图4-12所示。
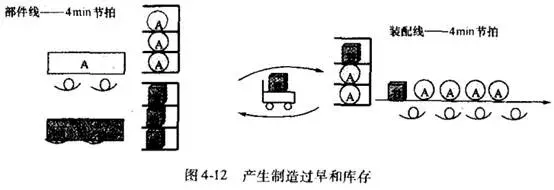
(3)为了解决上述问题,如果将部件线的生产节拍调整到8min,各工位无等待现象,并且生产能力配置可减少50%(如部件线操作人员只需1人)。但是后工序的装配线在使用其中一种部件时,另一种部件会有中间库存。例如,后工序的装配线在使用部件B时,A部件线还在生产,但A部件未被领取,因此出现中间库存,最多时会出现2个A部件,如图4-13所示。
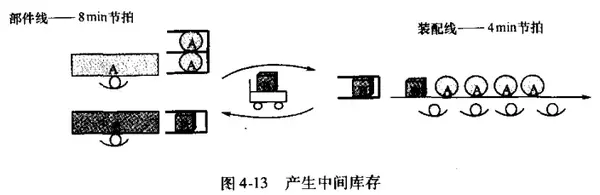
(4)若对后工序进行品种均衡,按照“A-B-A-B-A-…”的循环顺序进行生产,如图4-14所示。这样可消除库存和等待,同时生产能力配置可以减少50%。
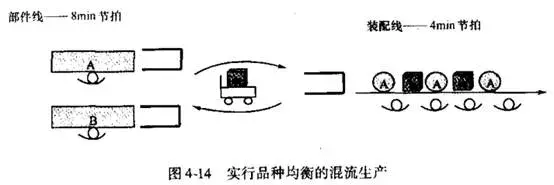
案例二:图4-15为生产a、b、c三种车型装配线。a车型作业时间是4.2min,b车型3.8min,c车型4.0min,根据生产需求,装配线的平均节拍是4min,如果采取连续生产方式,如图4-15a所示。整个装配线需要按最大节拍4.2min(生产a车型)配置人员,但当最小节拍3.8min(生产b车型)时则会产生等待,从而造成人员的浪费。
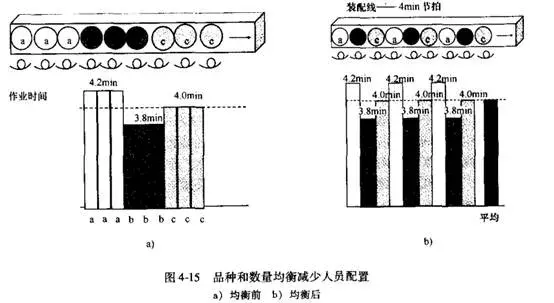
对装配线生产进行品种均衡即采用混流生产,如图4-15b所示。操作者尽管在生产节拍 56较长的a车型时压位,但是紧接着就生产节拍较短的b车型,这样刚刚达到平均节拍,因此可以按平均节拍配置人员。这种适合于人员配置的生产方式,既能合理配置人员,又能满足生产,消除浪费。
总之,在混流装配线上,即使各个品种的产品在每个工作站的平均负荷都达到均衡,但是对每个品种来讲,随着投产顺序的不同,不同品种的产品在不同工作站中负荷各不相同,工作站中闲置与超载现象时常发生。而工作站的闲置与超载均会造成装配流水线效率低下,尤其是超载现象发生时,劳动强度大的工人为了赶上生产线的运行节拍,常常忽视了产品质量。这样不仅影响到产品的质量而且增加了生产成本,降低了效率。据美国有关资料统计,即使在美国这样工业发达的国家,在工业装配生产中平均要有5%~10%的生产时间是浪费在平衡延迟上。而采用品种均衡后,通过把所需工时多的产品、所需工时一般的产品、所需工时少的产品合理地搭配,均衡地进行流水混流生产,可有效地解决装配线平衡问题。
综上所述,实施均衡化是实现准时化生产的基础,它有五个方面的优点:
(1)零部件使用量稳定。因为在每个循环内生产的种类及数量都一样,所以向前工序领取或向零部件仓库领取的零部件类别和数量也较稳定,向供应商订货的类别及数量也较稳定。
(2)设备和人力负荷稳定化,提高利用率。各个生产阶段所需求的种类及数量稳定,会使各工序以及供应商的生产负荷也较稳定,设备和人力利用率也较高。
(3)在制品与库存大大减少。在制品库存量与生产批量成正比,均衡化生产需减少批量,因此库存也将大量减少。
(4)提高了对市场的反应速度。均衡化生产减少批量,使每一个产品制造周期大幅缩短,大大提高了市场响应能力。
(5)使工人操作更加熟练。工人在批量较大的生产情况下,一般各品种每月重复生产一次,由于相隔时间长,在切换做另一产品的初期时,往往作业效率低,易产生品质问题。在均衡生产的条件下,工人每天都要生产不同种类的产品,通过这种高频率、切换的生产方法,使得工人对这几种产品的操作越来越熟练,有助于提高劳动效率。
实现均衡化生产需要注意以下几个方面的问题:
(1)不同的产品其作业方式多少会有不同的地方,所以事前的训练是很重要的。在实际作业中,很容易有错误的动作和拿错部件的现象。如何用防错法的原理来避免,成为一个必须研究的课题。
(2)与前工序相对,小批量生产中的频繁的物品取用是必要的,为了让库存和出品时间缩短,所在前工序中有必要进行小批量的生产,缩短程序的运行时间,因此增加了生产品种的切换次数,从而切换总时间大幅度地增加。企业必须努力采用快速转换技术补偿这部分的时间损失。
(3)不同的零部件生产除了作业不同外,有时使用的设备、夹具、模具或工具也会有不同的地方。因此,除了要导入快速转换技术外,也可以考虑设计通用的工装、夹具来整合不同的产品,以配合适当的机器设备,一般以引入应用柔性生产系统(Flexible ManufacturingSystem,FMS)和成组技术(Group Technology,GT)的生产机器配置技术为宜。为了实现这些手段,需要一定技术和资金,这有时会超越一般中小企业的能力。
(4)在市场需求量大幅度变动的时候,生产量的适应也会变得很困难。例如以月安排的生产计划,供应商也是据此安排生产供货。但是实际的需求量与原先的计划量差异太大时,供应商的生产就会受到很大影响,而无法正常供货。针对这个问题,可以采取两种办法:①设法将变动的幅度控制在10%以内。每天必须从市场上的销售点收集市场需求的信息,随时更新市场需求量的预测。一般的以一个月预测一次的方式无法及时反应市场的变化,最好做到每10天一次的“旬预测”。根据旬预测的生产计划与实际的需求量差异量通常可以维持在10%以内。②如果要结束某种特定类型产品的生产,必须事先通知供应商,并对相关损失进行补偿。