日本丰田公司在2018年《财富杂志》500强中高居第6位,位列装备型制造业的首位。营业收入与利润总额在整个汽车行业排名第一。不仅利润是大众公司的将近2倍,比排名6~10的车厂的总和还要多。在2018年全球销量最高的15款车型中,丰田一家就占据了4款
丰田的成功并非源于它鹤立鸡群的研发实力、也绝非是拥有超群的高科技,而是扎根于它首创的新一代制造模式TPS。在丰田公司出版的《丰田之路,2001》的同时,他们也公开分享了当今著名的TPS中所称的DNA。“丰田之路”建立在两大支柱之上:持续改善、对人的尊重
源于丰田制造模式TPS的精益制造LP,自1990年正式面世以来,风靡全球,成为了全世界企业与组织的标杆。从汽车行业推广到其他制造业、从制造业推广到服务、零售等其他行业、从制造系统推广到研发、销售、订单处理、行政等所有的职能,足见精益思想之强大,也代表了人类制造业目前的最高水平与境界
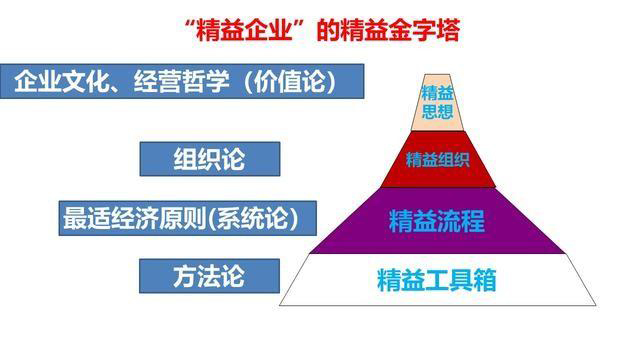
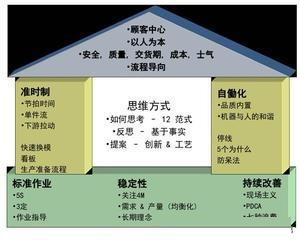
丰田TPS之屋
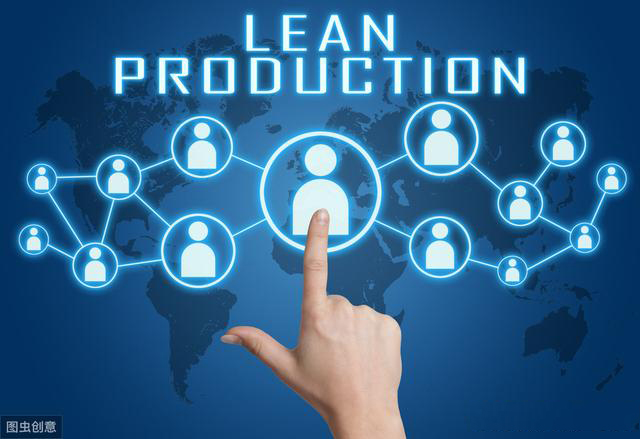
01、TPS的腾空出世与精益的崛起
1、20世纪50年代,日本全行业一年的汽车产量还不及美国几大巨头3天的产出。但经过20多年的潜心发展,美国人惊奇地发现,道路上出现了越来越多的日本汽车。为此美国麻省理工学院MIT发起了国际汽车计划IMVP,对日本汽车业的崛起进行彻底的分析与研究。 精益生产( Lean Production)是美国麻省工学院专家经过5年的研究之后,给予丰田生产方式的名称,以区别于人类已有的手工艺生产及大规模生产方式,简称LP。在J.沃马克、D.琼斯、D.鲁斯的经典名著《改变世界的机器》中首次使用了LP,并迅速推广到全世界
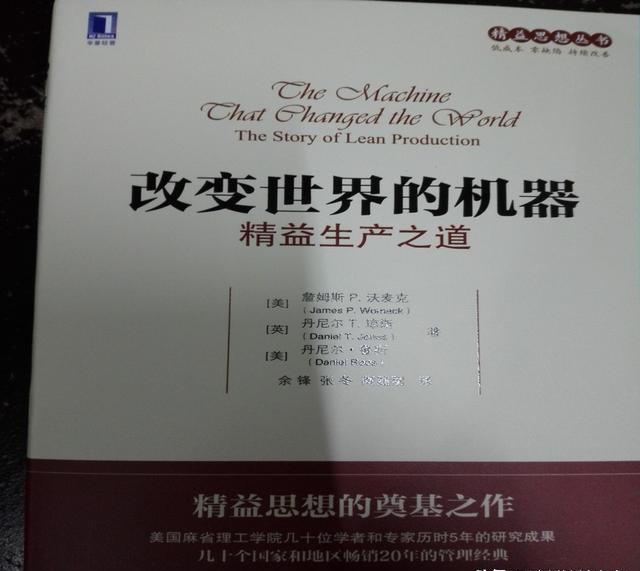
2、 精益生产雏形在20世纪70年代起源于日本丰田汽车公司。 丰田生产方式最终目标就是提高全公司的利润。为实现目标,大野耐一把客户原点、消除浪费、降低成本(节流增效)就成为最基本目标(Toyota Production System)简称TPS。它是精益制造的雏形、也是最佳的实践。 当时丰田已经成为超越美国、欧洲所有汽车制造商,成为行业的标杆
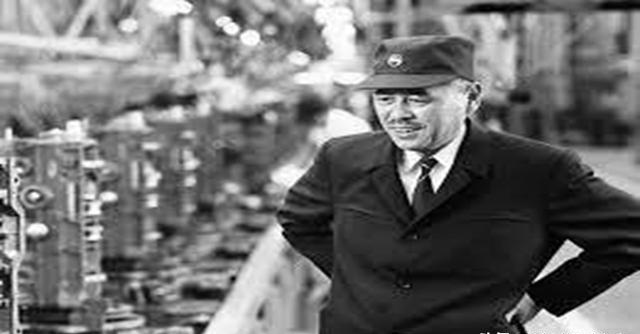
TPS的缔造者:大野耐一
02、TPS及LP的核心思想
1、日本丰田TPS的4大核心
- “客户原点”的价值观
彻底抛弃“绩效与财务功利主义”
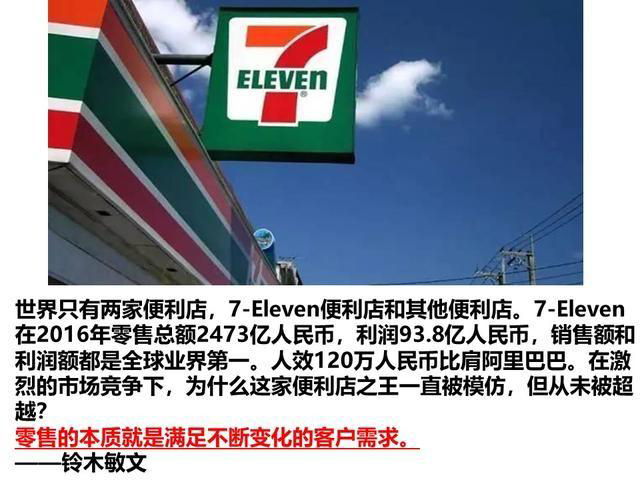
- “消除全流程浪费、节流增效”的经营战略
认知广义的隐形浪费:大野耐一的7大浪费与日本的3M Loss理论
MUDA、MURA、MURI
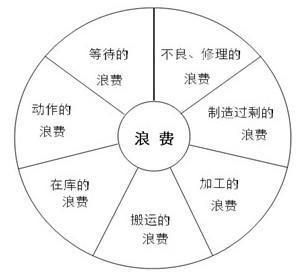
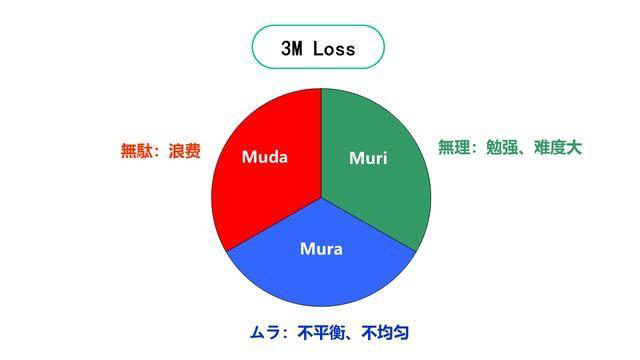
- 以人为本、尊重个人、智慧创造
- 持续改进、追求完美的变革意识
争当“乌龟”、不做“兔子”
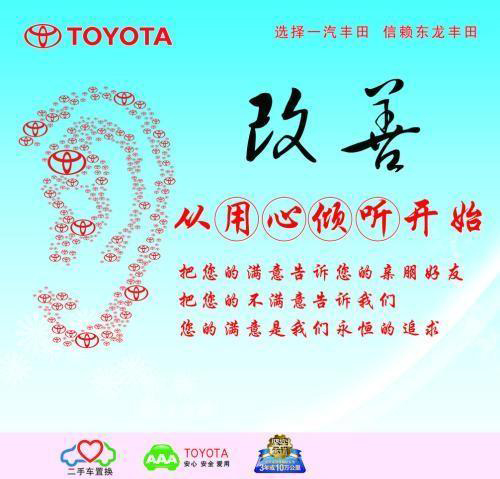
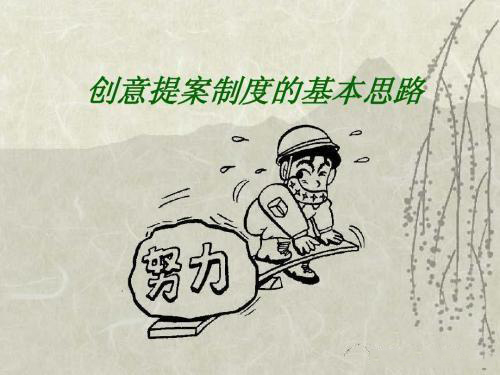
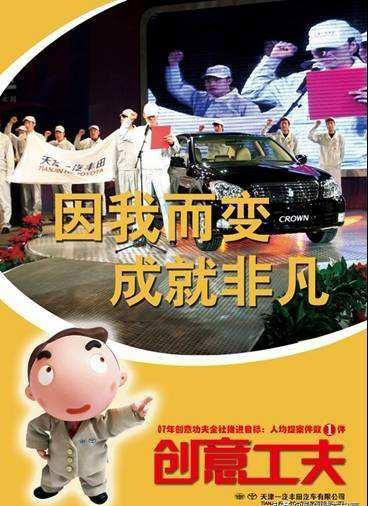
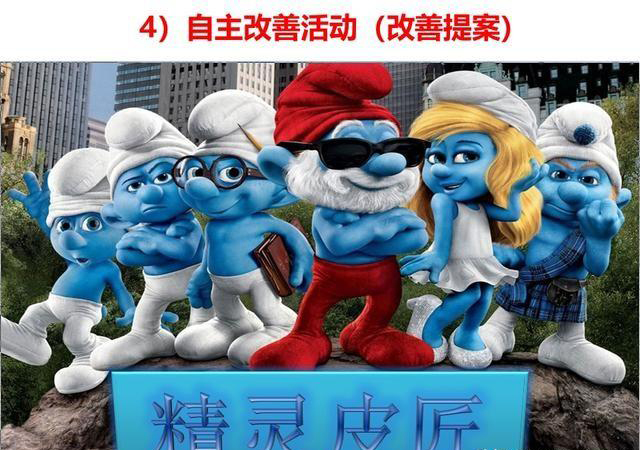
- 在丰田公司出版的《丰田之路,2001》的同时,他们也公开分享了当今著名的TPS中所称的DNA。“丰田之路”建立在两大支柱之上:持续改善、对人的尊重
2、 J.Womack与D.Jones的“精益5大思想”
- 1996年, J.Womack与D.Jones出版了名著《精益思想》,首次提出了精益制造的“5大核心思想”,至今仍被奉为经典
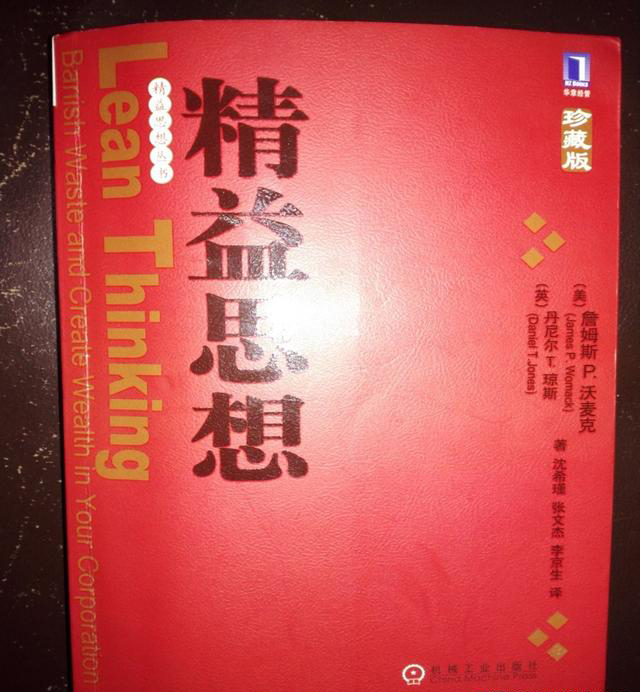
- “客户原点”的价值(Value)
- 价值流链(Value Stream & Chain)
解决问题任务
信息管理任务
物质转化任务
- 流动(Flow)
- 拉动(Pull)
- 尽善尽美、追求卓越(Perfect)
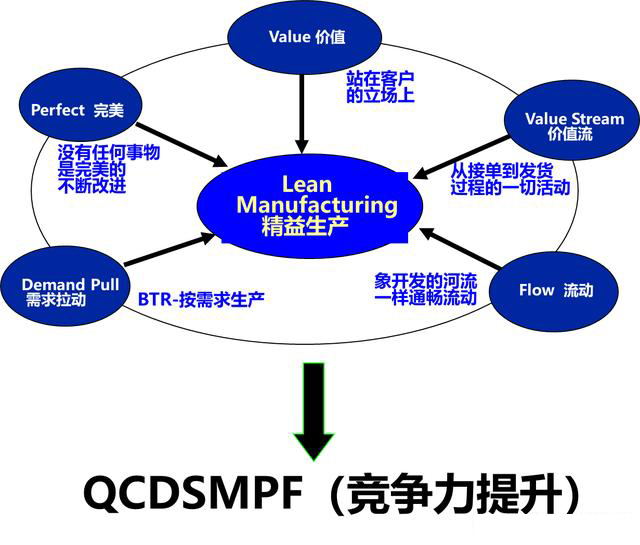
03、LP的新高度与至臻境界
1、精益不再局限于制造流程,而是扩展至制造型企业运作的整个流程(研发、销售、供应链、物流、订单处理)
- 不再局限“精益制造”,而是强调“精益企业”
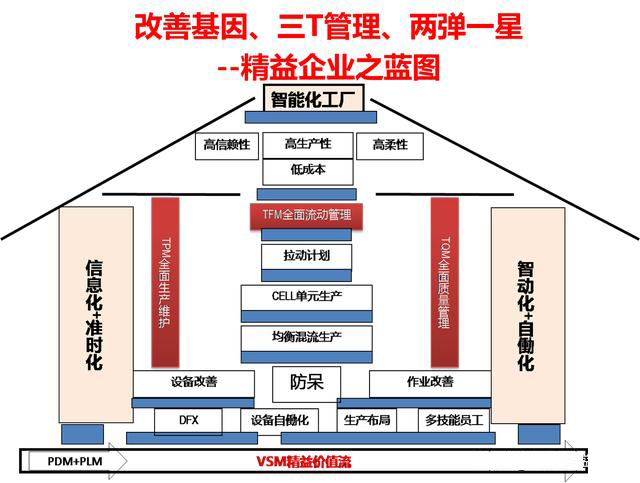
- 改善是“基因”,但改善活动已经提升至运用高级工具“价值流图VSM“进行全流程定量分析
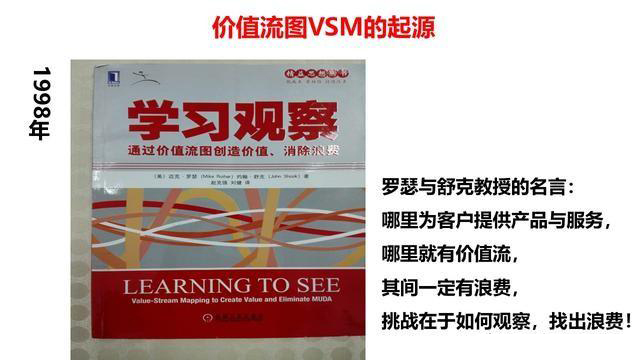
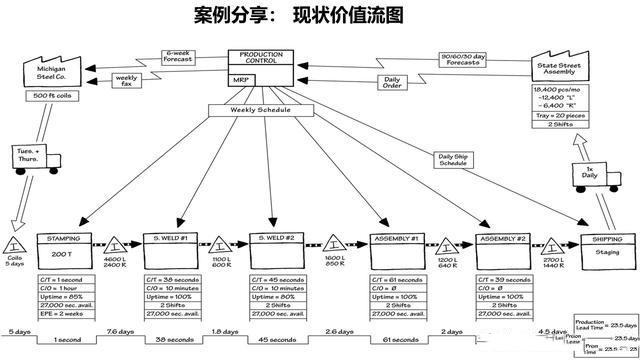
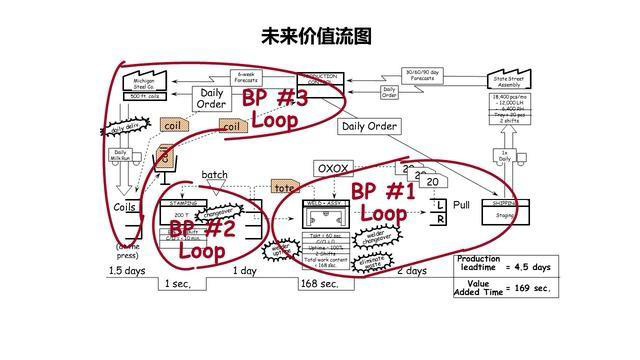
- 3T基础:TPM(全面生产性管理)、TQM(全面品质管理)、TFM(全面流动性管理)
- 2大支柱:JIT+信息化、自働化+智动化
- 不再局限在本企业,而且延伸至核心供应商的供应链管理SCM、核心合作商\经销商的价值链管理VCM
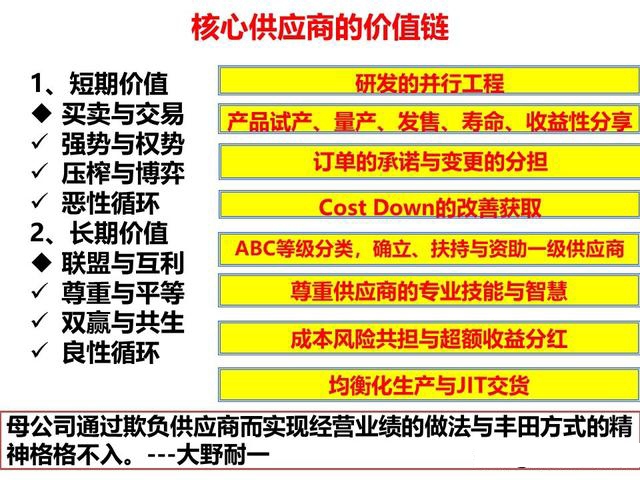
2、 已经推广到了众多其他行业。例如:零售业、服务行业(医疗、运输)、设计研发
3、 超越传统TPS、精益制造的4大深入
- 践行JIT、构建“全面流动性管理TFM“
产、供、销联动的PSI计划体系,彻底执行“按单生产”
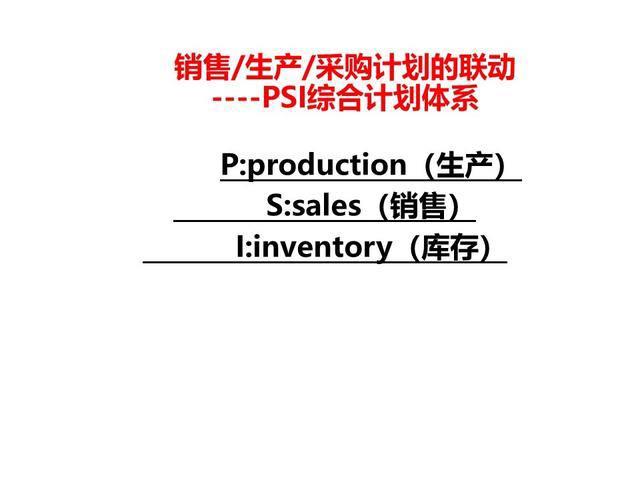
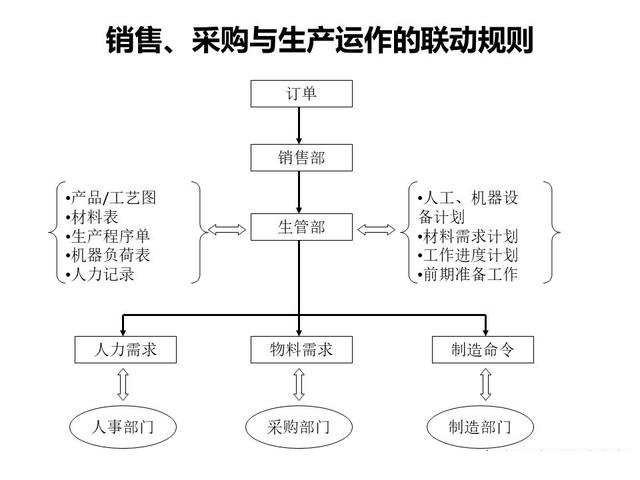
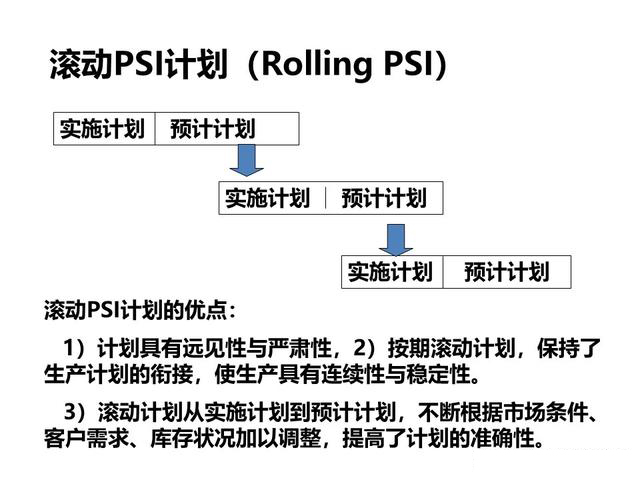
制造全流程的拉动式生产
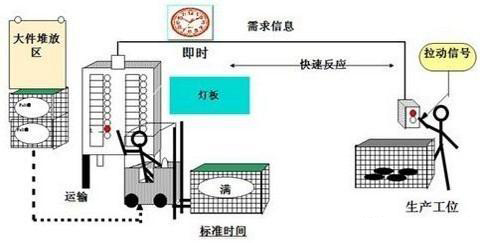
供应商的JIT供货
- 跨越ERP、导入“数字信息化管理“
MES(制造执行系统)
APS(高级计划与排产系统)
MDS(物料配送系统)
WMS(仓库智能管理系统)
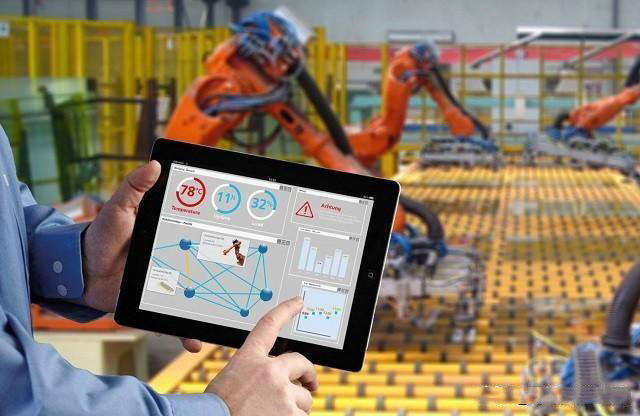
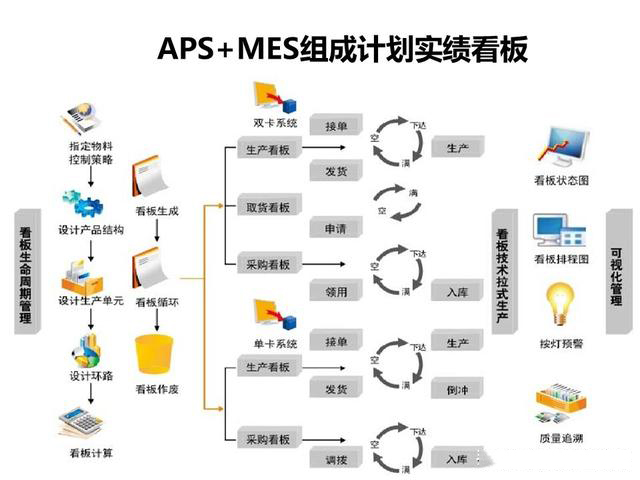
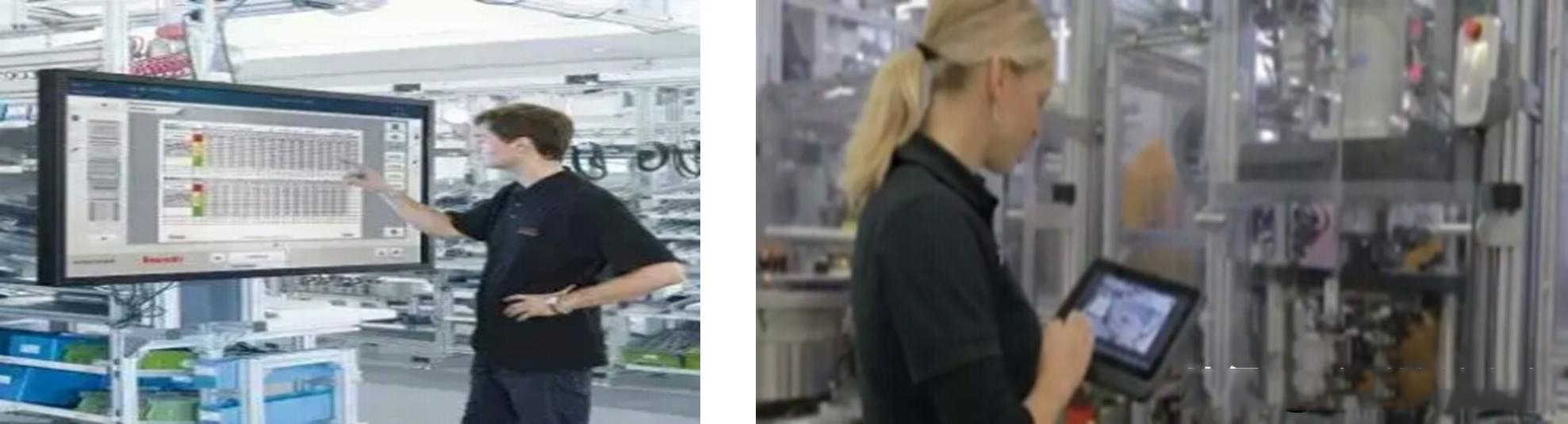
- 跨越自働化、步入“智动化“
简便自动化LCIA
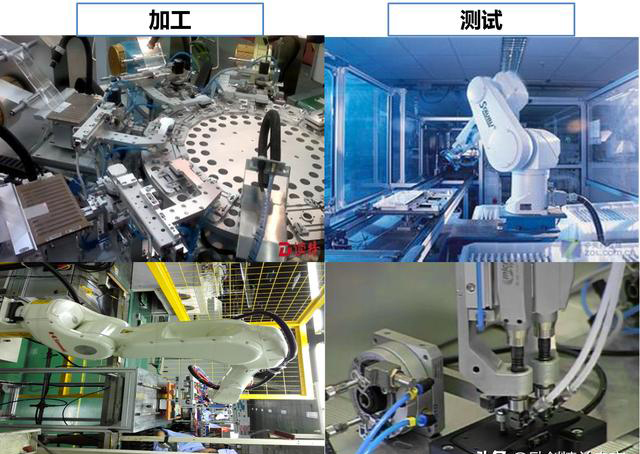
数字智动化
柔性化
智能设备
数字化设备
集成管理系统
设备物联网
准大数据
云处理中心
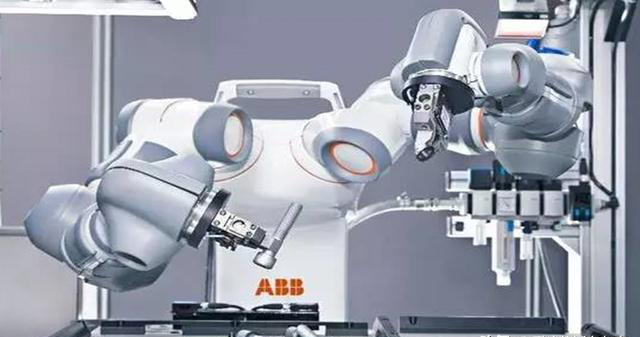
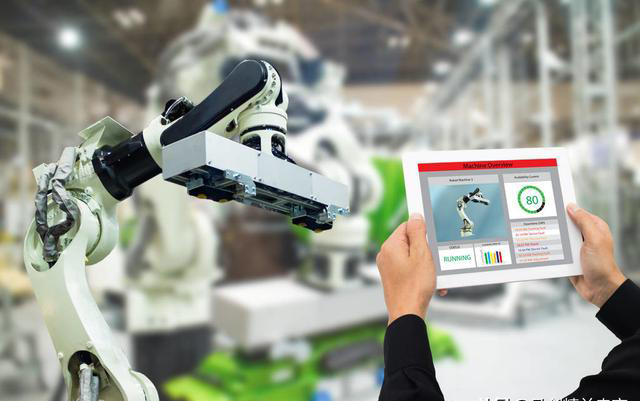
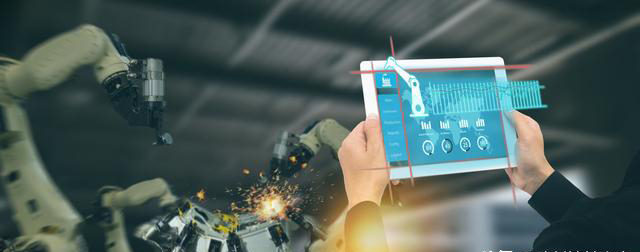
- 跨越3.0、步入“工业4.0”
装备智能化
产线智能化
车间智能化
工厂智能化
供应链智能化
服务智能化
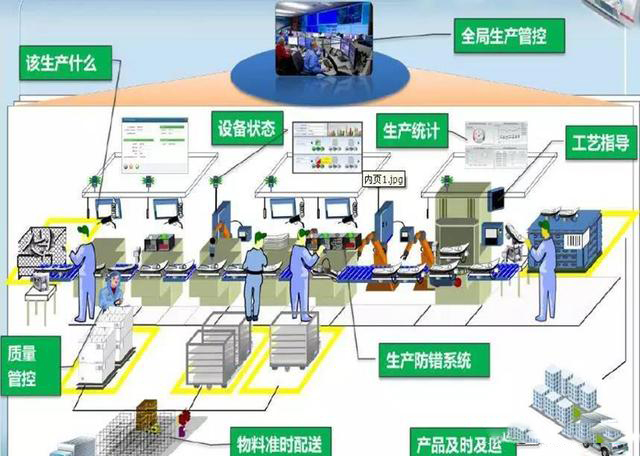
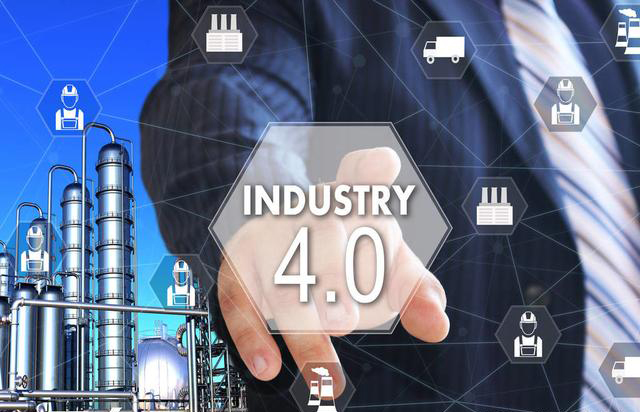
04、丰田新一轮竞争战略TNGA
1、日本丰田公司之所以成为全世界制造业的标杆企业,不是因为它在汽车制造全流程中所展现的高科技、新科技,而是因为它创建的“精益制造与管理”的企业体系。这个体系绝不迷信、迷恋高科技、新科技,而是坚守丰田之道的DNA:持续改进、对人的尊重!对于中国企业而言,绝对值得借鉴!
2、过去几十年间,丰田对于汽车生产制造的严谨态度名满天下,“看板”模式和消除浪费的理念奠定了丰田生产方式(TPS)的神圣地位,并被业内人士反复研究。不过丰田似乎对此并不在意,这一次带来TNGA平台,似是希望再次为日本汽车制造商赢得新的竞争优势,未雨绸缪,重新定义汽车制造的方方面面。
3、丰田天生就不是“技术男”,更不迷恋、迷信高科技、新技术。虽然豪华车型雷克萨斯、世界首款混合动力车型普锐斯的面世可谓惊世骇俗,但丰田一直认为“高效的研发组织、研发流程、研发的激励制度”才是成功的关键
4、新一轮的战略TNGA也是如此。它更强调“客户原点、资源整合、快速反应、智慧创造”的竞争策略
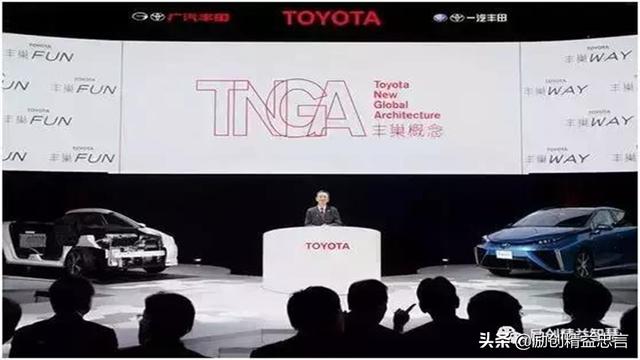
5、、急功近利,过分注重精益方法、工具,严重忽略精益组织、精益文化、持续改善文化或全员参与文化,注定失败,至少难以持续为继!
05、精益金字塔的修炼
1、精益金字塔
精益4层次、工具及流程优化只是最低的层别
2、精益体系8大维度
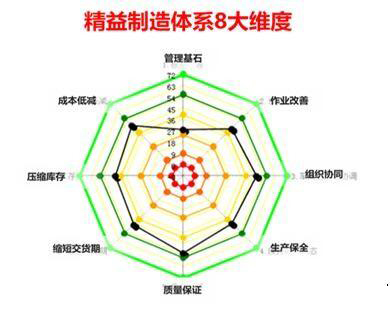
3、J.Womack与D.Jones在名著《精益思想》中给出了一个“普适时间标准”。5年的持续革新才能初见成效
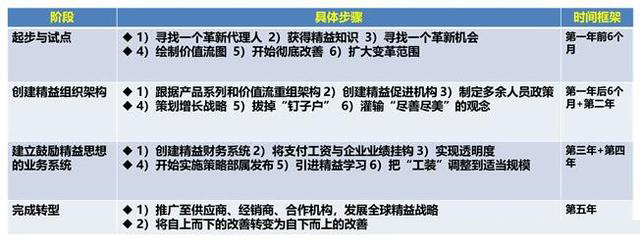
精益革新4部曲
- 精益革新是一场没有终点的旅程,急功近利绝不可能成功!